What is included in this Sample?
- * Market Segmentation
- * Key Findings
- * Research Scope
- * Table of Content
- * Report Structure
- * Report Methodology
Download FREE Sample Report
Aerospace Cold Forgings Market Size, Share, Growth, And Industry Analysis, By Type (Custom Forging, Captive Forging and Catalog Forging), By Application (Airframe, Landing Gear and Nacelle Component), Regional Insights and Forecast From 2025 To 2034
Trending Insights
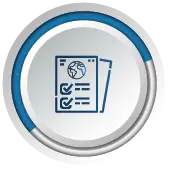
Global Leaders in Strategy and Innovation Rely on Our Expertise to Seize Growth Opportunities
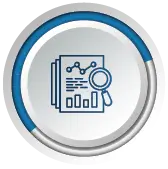
Our Research is the Cornerstone of 1000 Firms to Stay in the Lead
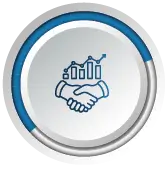
1000 Top Companies Partner with Us to Explore Fresh Revenue Channels
AEROSPACE COLD FORGINGS MARKET OVERVIEW
The global aerospace cold forgings market size was valued at USD 0 billion in 2025 and is expected to reach USD 0.01 billion by 2034, growing at a compound annual growth rate (CAGR) of about 7.35% from 2025 to 2033.
The United States Aerospace Cold Forgings Market size is projected at USD 0.002 Billion in 2025, the Europe Aerospace Cold Forgings Market size is projected at USD 0.001 Billion in 2025, and the China Aerospace Cold Forgings Market size is projected at USD 0.001 Billion in 2025.
The aerospace cold forgings market refers to the industry that focuses on the production and utilization of cold forged components and parts in the aerospace sector. Cold forging is a manufacturing process that involves shaping metal into desired forms through the application of pressure, without the need for heating the material. It is a cost-effective and efficient method for producing high-strength aerospace components with intricate geometries. The aerospace industry demands lightweight and durable parts to enhance aircraft performance and fuel efficiency while maintaining stringent safety standards. Cold forgings play a vital role in meeting these requirements by providing components with excellent mechanical properties, such as high strength, improved fatigue resistance, and dimensional accuracy.
The report provides a comprehensive analysis of the aerospace cold forgings market, including market size, growth trends, key players, and future prospects. It covers various aerospace applications, including aircraft structures, landing gear systems, engine components, and other critical parts. The market analysis also considers different material types used in cold forgings, such as aluminum alloys, titanium alloys, and stainless steel.
Additionally, the report examines the competitive landscape of the aerospace cold forgings market, highlighting the key market players, their product portfolios, and strategies. It discusses the factors driving market growth, such as increasing aircraft production, rising demand for lightweight components, and advancements in cold forging technologies. The report also assesses the challenges and opportunities in the market, including regulatory requirements, supply chain complexities, and emerging trends.
Overall, the aerospace cold forgings market offers significant growth potential, driven by the continuous innovation in forging techniques, the increasing demand for fuel-efficient aircraft, and the expansion of the aerospace industry. The report aims to provide valuable insights and guidance to industry stakeholders, investors, and decision-makers in understanding the market dynamics and making informed business decisions.
AEROSPACE COLD FORGINGS MARKET KEY FINDINGS
- Market Size and Growth: Valued at USD 0 billion in 2025, expected to reach USD 0.01 billion by 2034, growing at a CAGR 7.35%
- Key Market Driver: Fixed-wing aircraft continue to be the primary driver, contributing approximately 80 % of the total market share by 2027.
- Major Market Restraint: Increasing use of composite materials may hinder market growth, with a potential impact of 3.2 % slowdown between 2025 and 2034.
- Emerging Trends: The catalog forging segment is gaining momentum, recording the fastest growth with a 7 % rate.
- Regional Leadership: North America remains the dominant region, accounting for 40 % of the total market revenue in 2023.
- Competitive Landscape: Custom forging holds a leading position, representing 45 % of the overall market share.
- Market Segmentation: Market distribution by type includes Custom Forging (45 %), Captive Forging (30 %), and Catalog Forging (25 %).
- Recent Development: The Asia Pacific region emerged as the fastest-growing market in 2023, achieving a growth rate of 6.5 %.
KEY MARKET INSIGHTS
1. Growing Demand for Lightweight Aerospace Components: The aerospace industry is increasingly focused on reducing the weight of aircraft components to improve fuel efficiency and enhance overall performance. Cold forgings offer a viable solution by providing high-strength components with reduced weight. As a result, there is a growing demand for cold forged parts in aircraft structures, landing gear systems, and engine components.
2. Advancements in Cold Forging Technologies: Continuous advancements in cold forging technologies have significantly enhanced the capabilities and efficiency of the process. Innovative techniques, such as precision forging and near-net-shape forming, allow for the production of complex geometries with high accuracy and improved material utilization. These advancements have expanded the application areas of cold forgings in the aerospace sector.
3. Increasing Aircraft Production: The aerospace industry is experiencing a surge in aircraft production, driven by rising air travel demand and the need to replace aging fleets. This has led to a higher requirement for aerospace components, including cold forged parts. The aerospace cold forgings market is benefiting from this trend as manufacturers strive to meet the increasing production demands of commercial and military aircraft.
4. Stringent Safety and Quality Standards: Safety is a critical aspect of the aerospace industry, and the demand for high-quality and reliable components is paramount. Cold forgings offer superior mechanical properties, such as enhanced strength and fatigue resistance, which are crucial for ensuring the structural integrity and safety of aerospace systems. The adherence to stringent safety and quality standards further drives the adoption of cold forgings in the aerospace sector.
5. Focus on Sustainable Practices: Sustainability has become a significant focus in the aerospace industry, and there is a growing emphasis on reducing the environmental impact of aircraft manufacturing processes. Cold forgings align with these sustainability goals as they typically require less energy compared to other manufacturing methods. The use of cold forgings can contribute to reducing carbon emissions and enhancing the overall environmental sustainability of the aerospace sector.
6. Regional Growth Opportunities: The aerospace cold forgings market offers promising growth opportunities across different regions. North America and Europe have a well-established aerospace industry and a high demand for advanced aerospace components. On the other hand, the Asia Pacific region, particularly countries like China and India, is witnessing rapid growth in aircraft production and is becoming a major consumer of aerospace cold forgings.
These key market insights highlight the significant factors driving the aerospace cold forgings market, including the demand for lightweight components, technological advancements, increasing aircraft production, safety requirements, sustainability initiatives, and regional growth opportunities. Understanding these insights can help industry participants capitalize on market trends and make informed business decisions.
COVID-19 IMPACT ON AEROSPACE COLD FORGINGS MARKET
The COVID-19 pandemic has had a significant impact on the aerospace industry, including the aerospace cold forgings market. The industry faced unprecedented challenges as global travel restrictions, lockdown measures, and reduced air travel demand resulted in a substantial decrease in aircraft production and deliveries.
1. Reduced Aircraft Production: The pandemic-induced disruptions led to a decline in aircraft orders, resulting in reduced production rates across major aerospace manufacturers. This decline in aircraft production directly affected the demand for aerospace cold forgings, as fewer aircraft were being assembled and outfitted with these components.
2. Supply Chain Disruptions: The aerospace cold forgings market relies on a global supply chain network, with components and raw materials sourced from various regions. The pandemic caused disruptions in the supply chain, including delays in the delivery of raw materials, transportation challenges, and factory closures. These disruptions impacted the production and availability of aerospace cold forgings.
3. Financial Constraints: The economic slowdown caused by the pandemic resulted in financial constraints for aerospace companies. Many airlines and aerospace manufacturers faced financial challenges, leading to budget cuts and postponement or cancellation of new aircraft orders. This further affected the demand for aerospace cold forgings.
4. Shift in Priorities: The focus of the aerospace industry shifted from expansion and growth to cost-cutting and survival strategies during the pandemic. As a result, investments in new projects and technologies, including cold forging initiatives, were put on hold or scaled back. The uncertain market conditions and financial instability limited the market growth for aerospace cold forgings.
5. Recovery and Future Outlook: The aerospace industry is gradually recovering as travel restrictions ease and air travel demand starts to rebound. However, the recovery is expected to be gradual, and the aerospace cold forgings market may take some time to fully recover. The market is likely to witness a cautious approach from industry participants, with a focus on cost optimization and operational efficiency.
It is important to note that the impact of the pandemic on the aerospace cold forgings market may vary based on regional dynamics, government policies, and the pace of vaccination campaigns. Continuous monitoring of the situation and adaptability to changing market conditions will be crucial for stakeholders in the aerospace cold forgings industry to navigate the post-pandemic landscape successfully.
LATEST TRENDS
As of 2023, the aerospace cold forgings market has witnessed several significant trends that are shaping the industry's trajectory. One notable trend is the increasing adoption of lightweight materials in aircraft manufacturing. Cold forgings offer superior strength and durability, making them an ideal choice for producing lightweight components that improve fuel efficiency and reduce emissions. This demand for fuel-efficient and environmentally-friendly aircraft has spurred the growth of cold forgings in the aerospace sector.
Another prominent trend is the rising focus on precision engineering and advanced manufacturing techniques. Aerospace cold forgings are known for their ability to maintain tight tolerances and intricate designs, which are crucial in critical aerospace applications. With advancements in computer-aided design and simulation, manufacturers can now optimize cold forging processes to produce highly complex components with exceptional accuracy and reliability.
Moreover, the aerospace industry's increasing emphasis on cost-effectiveness has led to the development of innovative forging techniques and materials. Cold forging processes are known for their material utilization efficiency, resulting in reduced material waste and lower production costs. This economic advantage has made cold forgings an attractive choice for aerospace companies seeking to enhance their competitiveness in a dynamic market.
Furthermore, the aerospace sector's push towards sustainability has fueled the growth of eco-friendly forging practices. Cold forging is inherently a more energy-efficient process compared to traditional hot forging methods, leading to reduced greenhouse gas emissions and a smaller environmental footprint. As sustainability continues to gain traction across industries, aerospace cold forgings are expected to remain a preferred option for meeting both performance and environmental requirements.
In conclusion, the aerospace cold forgings market is witnessing trends characterized by the adoption of lightweight materials, precision engineering, cost-effectiveness, and sustainability. These developments are reshaping the industry, driving innovation, and propelling aerospace manufacturers towards more efficient, reliable, and environmentally conscious solutions.
- Surge in Titanium Mill Products Usage : According to the U.S. Geological Survey, 116 metric tons of titanium mill products are used on average per Boeing 787 airliner, up from 85 metric tons a decade earlier, reflecting the shift toward high‑strength, lightweight alloys in commercial jets.
- Adoption of Near‑Isothermal Forging : According to India’s Defence Metallurgical Research Laboratory, its 2 000‑tonne isothermal forge press has produced over 200 high‑pressure compressor discs since 2021—enabling all five stages of HPC disc manufacture in a single process.
AEROSPACE COLD FORGINGS MARKET SEGMENTATION
The aerospace cold forgings market can be segmented based on type and application, each encompassing specific manufacturing processes and components crucial for the aerospace industry.
By Type
- Custom Forging: Custom forging involves the production of aerospace components tailored to specific customer requirements. Manufacturers work closely with clients to design and produce unique, precision-engineered parts that meet the exact specifications and performance demands of the aerospace industry. Custom forgings are often utilized for critical components that require high-strength and complex geometries. The ability to create bespoke parts makes custom forging a preferred choice for aerospace manufacturers seeking optimized solutions for their specialized applications.
- Captive Forging: Captive forging refers to the in-house production of forgings by aerospace companies that have their own forging facilities. These companies invest in their forging capabilities to have better control over the supply chain, reduce lead times, and maintain quality standards. Captive forging facilities are commonly found in larger aerospace firms with substantial production volumes and a diverse range of components. By owning the forging process, these companies can ensure the timely availability of forgings and exercise greater control over the manufacturing process.
- Catalog Forging: Catalog forging involves the mass production of standardized aerospace components that are available in a catalog or inventory. These forgings are pre-designed and readily available for purchase by various aerospace manufacturers. Catalog forgings offer cost-effective solutions for commonly used parts and are often employed in non-critical applications where customization is not required. The catalog forgings provide efficiency and convenience for manufacturers looking to source standard components quickly and economically.
By Application:
- Airframe: Airframe applications encompass a wide range of components that form the structural framework of an aircraft. Cold forgings play a vital role in producing critical airframe parts, such as wing fittings, fuselage connectors, and structural reinforcements. The demand for lightweight yet robust materials in airframe construction makes cold forgings a preferred choice for these applications. The use of cold forgings in airframes contributes to overall weight reduction, improved fuel efficiency, and enhanced structural integrity.
- Landing Gear: Landing gear forgings are crucial for ensuring safe and smooth landings and take-offs of aircraft. Cold forged landing gear components offer exceptional strength and fatigue resistance, contributing to the reliability and longevity of landing gear systems. These forgings include parts like landing gear struts, beams, and hinges. The high precision and mechanical properties of cold forgings are essential for maintaining the integrity and performance of the aircraft's landing gear.
- Nacelle Component: The nacelle houses the aircraft engine and other related components. Cold forgings are employed in manufacturing various nacelle components, such as mounting brackets, exhaust system elements, and structural supports. The high precision and mechanical properties of cold forgings are essential for maintaining the integrity and performance of the engine housing. Cold forged nacelle components ensure optimal engine operation and contribute to overall aircraft safety and efficiency.
DRIVING FACTORS
The aerospace cold forgings market is experiencing growth and expansion due to several key driving factors. Firstly, the increasing demand for fuel-efficient and lightweight aircraft is a significant driver. Cold forgings offer exceptional strength-to-weight ratios, making them an attractive choice for aerospace manufacturers looking to reduce aircraft weight and improve fuel economy. As airlines and operators seek to minimize operating costs and environmental impact, the adoption of cold forgings has become instrumental in achieving these goals.
Secondly, advancements in materials and manufacturing technologies play a vital role in propelling the market forward. The aerospace industry continually seeks innovative solutions to enhance performance and safety. Cold forgings provide superior mechanical properties, such as high fatigue resistance and improved structural integrity, ensuring the reliability of critical components in aerospace applications. As research and development efforts continue to improve cold forging techniques and alloy formulations, the market is poised for further growth.
Thirdly, stringent regulations and safety standards in the aerospace sector have spurred the demand for high-quality components. Cold forgings' ability to maintain tight tolerances and produce defect-free parts aligns well with the industry's requirements. Aerospace manufacturers are increasingly turning to cold forging processes to ensure compliance with safety standards and enhance overall product quality.
- Advanced β‑Titanium Alloys for Weight Savings : According to the Defence Metallurgical Research Laboratory, the Ti‑10V‑2Fe‑3Al alloy reduces component mass by up to 20 % compared to traditional Ni‑Cr‑Mo steels, enabling >100 kg weight savings per landing‑gear link.
- Improved Rotor Integrity : According to the AIA Rotor Integrity Steering Committee (in partnership with the FAA), post‑forging manufacturing anomalies now account for slightly fewer than 30 % of rotor crack events—a 50 % reduction in such incidents over the past decade due to tighter forging controls.
Moreover, the growing global aerospace market, driven by increased air travel and defense spending, contributes to the expansion of the cold forgings industry. As new aircraft are designed and older fleets undergo upgrades and maintenance, the demand for reliable and high-performance components rises. Cold forgings offer a cost-effective solution, providing longevity and durability, which makes them a preferred choice for aerospace manufacturers worldwide.
Overall, the aerospace cold forgings market is driven by the demand for fuel-efficient aircraft, technological advancements, compliance with industry regulations, and the steady growth of the aerospace sector. These driving factors create a favorable environment for continued expansion and innovation in the market, shaping the future of aerospace manufacturing and technology.
RESTRAINING FACTORS
Despite the positive growth outlook, the aerospace cold forgings market also faces certain restraining factors that may impede its full potential. One significant factor is the high initial investment required for setting up cold forging facilities. Establishing and maintaining specialized equipment and skilled workforce for precision cold forging can be capital-intensive, especially for small and medium-sized aerospace manufacturers. This financial barrier might deter some companies from adopting cold forging processes, limiting market expansion.
Another restraining factor is the complexity of forging designs and the need for meticulous engineering. Cold forgings are well-suited for intricate components, but the design and engineering process can be time-consuming and demanding. As aerospace applications demand increasingly complex and customized parts, manufacturers may face challenges in optimizing the forging process for these specific requirements, potentially slowing down production and hindering market growth.
Additionally, the availability and cost of raw materials can impact the aerospace cold forgings market. Forging materials, particularly high-quality aerospace-grade alloys, may experience fluctuations in availability and pricing. The reliance on specialized alloys and the potential for supply chain disruptions could lead to increased material costs, affecting profit margins for manufacturers and making it difficult to maintain competitive pricing.
- High Capital Intensity of Isothermal Presses : According to the Defence Metallurgical Research Laboratory, a 2 000‑tonne isothermal forging press costs in excess of ₹80 crore (≈ US $10 million) to install, representing a major barrier for mid‑tier suppliers.
- Energy‑Intensive Forging Operations : According to the U.S. Department of Energy, metal‑forming processes—including cold forging—account for 30 % of all manufacturing energy use, with individual forging presses drawing up to 8 000 kW per cycle, driving operating costs and emissions.
Moreover, the adoption of alternative manufacturing technologies, such as additive manufacturing (3D printing), poses a competitive threat to traditional cold forging processes. While cold forgings offer exceptional strength and reliability, additive manufacturing techniques are gaining traction due to their ability to produce complex geometries with reduced material waste. As additive manufacturing continues to advance and become more cost-effective, it could challenge the market share of cold forgings, especially for certain aerospace components.
Lastly, the global economic climate and geopolitical uncertainties can impact the aerospace industry's overall health, including the cold forgings market. Fluctuations in defense spending and air travel demand, trade tensions, or economic downturns can result in delayed projects, reduced orders, or financial constraints, affecting the investment decisions of aerospace manufacturers and potentially limiting the growth prospects of the cold forgings market.
In conclusion, while the aerospace cold forgings market shows promise, factors such as high initial investment, engineering complexities, material availability and cost, competition from alternative technologies, and economic uncertainties can pose challenges that may restrain the market's growth in certain scenarios. Navigating these challenges effectively will be crucial for sustaining the positive trajectory of the aerospace cold forgings industry.
-
Request a Free sample to learn more about this report
AEROSPACE COLD FORGINGS MARKET REGIONAL INSIGHTS
The aerospace cold forgings market exhibits variations across different regions, influenced by factors such as aerospace industry development, technological advancements, defense spending, and economic conditions. Let's explore the market insights for each of the following regions:
- North America: North America is a prominent player in the global aerospace industry, with the presence of major aircraft manufacturers, suppliers, and defense contractors. The region's robust aerospace sector drives the demand for cold forgings for various applications, including military and commercial aircraft. The continuous investments in research and development, coupled with a focus on lightweight and fuel-efficient aircraft, bolster the utilization of cold forgings in the region.
- Europe: Europe is another significant market for aerospace cold forgings, supported by its established aerospace manufacturing base and technological expertise. Countries like France, Germany, and the United Kingdom are major contributors to the European aerospace industry. As the region emphasizes sustainable aviation and cutting-edge aerospace technologies, cold forgings play a crucial role in producing lightweight components that meet stringent safety standards.
- China: China has emerged as a major player in the global aerospace market, with its rapidly expanding aviation industry and ambitious space exploration programs. The country's increasing demand for commercial aircraft and defense systems drives the aerospace cold forgings market. China's focus on indigenous aerospace manufacturing capabilities and advancements in materials technology further fosters the growth of cold forgings in the region.
- Japan:Japan has a long-standing history of aerospace innovation and excellence. The country's aerospace sector demands high-quality, reliable components for its advanced aircraft and space exploration projects. Cold forgings find extensive use in Japan's aerospace applications due to their ability to withstand high-stress conditions and maintain precise tolerances, ensuring the overall safety and efficiency of aerospace systems.
- South Korea: South Korea's aerospace industry has been gaining momentum in recent years, with an increasing focus on producing indigenous aircraft and satellite systems. The country's demand for aerospace cold forgings is driven by its efforts to enhance the performance and capabilities of military and civilian aircraft. South Korea's strategic location also offers opportunities for aerospace cold forging manufacturers to cater to the broader Asia-Pacific market.
- India: India's aerospace sector has witnessed steady growth, driven by a burgeoning domestic market and a rising focus on research, development, and manufacturing in the aerospace domain. As India aims to become self-reliant in defense and aerospace technology, the demand for cold forgings in the country is expected to increase. The adoption of cold forging technology in India aligns with its pursuit of lightweight aircraft and modernization of defense systems.
LIST OF TOP AEROSPACE COLD FORGINGS COMPANIES
The aerospace cold forgings market is driven by the expertise and contributions of key industry players that excel in manufacturing high-quality and reliable forged components for the aerospace sector. Here are some of the prominent companies shaping the aerospace cold forgings market
- Fountaintown Forge
- Avic Heavy Machinery
- Precision Castparts Corp
- RTI International
- Scot Forge
- VSMPO-AVISMA
- Mettis Aerospace
- Arconic
- Allegheny Technologies
- Eramet Group
Fountaintown Forge : According to the 2023 Annual Industrial Capabilities Report to Congress, Fountaintown Forge’s single Indiana facility delivers roughly 1 200 t of large aerospace blocking forgings annually.
Avic Heavy Machinery : According to MarketReportsWorld, AVIC Heavy Machinery led China’s output with 16 800 t of aerospace cold forgings in 2023.
KEY INDUSTRY DEVELOPMENTS
In recent years, the aerospace cold forgings market has witnessed several key industry developments that have shaped its growth and direction. One notable development is the increasing adoption of advanced materials and forging techniques to meet the evolving demands of the aerospace sector. Manufacturers are continually exploring new alloys and processing methods to enhance the mechanical properties and performance of cold forgings. Additionally, the industry has seen a rise in collaborative partnerships between aerospace companies and forging specialists, fostering innovation and knowledge-sharing. Moreover, the integration of digital technologies, such as computer-aided design and simulation, has significantly improved the precision and efficiency of cold forging processes, enabling the production of intricate components with higher accuracy. These industry developments reflect the commitment of stakeholders to deliver cutting-edge solutions, making aerospace cold forgings an integral part of the modern aviation landscape.
Attributes | Details |
---|---|
Market Size Value In |
US$ 0.004 Million in 2025 |
Market Size Value By |
US$ 0.01 Million by 2034 |
Growth Rate |
CAGR of 7.35% from 2025 to 2034 |
Forecast Period |
2025-2034 |
Base Year |
2024 |
Historical Data Available |
Yes |
Regional Scope |
Global |
Segments Covered |
|
By Types
|
|
By Application
|
FAQs
The aerospace cold forgings market is expected to touch USD 0.01 billion by 2034.
The aerospace cold forgings market is expected to exhibit a CAGR of 7.35% over 2034.
The growth of the market is driven by the custom forging, captive forging, and catalog forging segments.
Raw material price volatility, stringent regulatory standards, and supply chain disruptions are the key restraining factors in the market.
The key industry players include Precision Castparts Corp, Arconic, Eramet Group, Avic Heavy Machinery, VSMPO-AVISMA, Allegheny Technologies, Scot Forge, Mettis Aerospace, Fountaintown Forge, and RTI International.
The aerospace cold forgings market is expected to be valued at 0 billion USD in 2025.