What is included in this Sample?
- * Market Segmentation
- * Key Findings
- * Research Scope
- * Table of Content
- * Report Structure
- * Report Methodology
Download FREE Sample Report
Aluminum Forgings Market Size, Share, Growth, And Industry Analysis, By Type (Conventional Aluminum Forgings, Custom Aluminum Forgings), By Application (Automotive, Aerospace & Military, Electrical Industry, Engineering Machinery, General Industrial Machinery), Regional Insights, and Forecast To 2033
Trending Insights
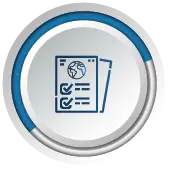
Global Leaders in Strategy and Innovation Rely on Our Expertise to Seize Growth Opportunities
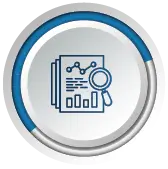
Our Research is the Cornerstone of 1000 Firms to Stay in the Lead
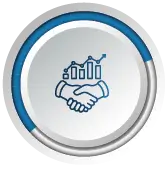
1000 Top Companies Partner with Us to Explore Fresh Revenue Channels
ALUMINUM FORGINGS MARKET OVERVIEW
Global aluminum forgings market size was USD 88.15 Billion in 2024 and market is projected to touch USD 150 Billion by 2033, exhibiting a CAGR of 6.08% during the forecast period.
Aluminum forgings refer to metal components made from aluminum alloy that is shaped through a process known as forging. Forging is a manufacturing process where a solid piece of metal is subjected to pressure and heat, typically in the form of hammering or pressing, to shape it into a desired form. They are produced by heating the aluminum alloy to a specific temperature, typically above its recrystallization temperature, and then applying force to shape it into the desired form using forging dies or tools. This process creates a strong and durable product with improved mechanical properties, such as increased strength, toughness, and fatigue resistance, compared to other manufacturing methods like casting. They are used in a wide range of industries, including automotive, aerospace, military, electrical, engineering, and general industrial machinery. They are preferred in applications where performance, safety, and lightweight properties are crucial, such as in aircraft parts, automotive components, and high-performance machinery.
Technological advancements in forging processes, such as computer-aided design (CAD), computer-aided manufacturing (CAM), and simulation tools, have revolutionized the way aluminum forgings are manufactured. These advancements have brought significant improvements in the efficiency and accuracy of forging processes, leading to reduced lead times, improved product quality, and increased productivity. Computer-aided design (CAD) has enabled manufacturers to create complex and precise designs for aluminum forgings, which can be easily modified and optimized to meet specific requirements. CAD software allows for 3D modeling, simulation, and analysis of the forging process, helping to identify potential issues and optimize the design for better performance. It has transformed the way forgings are produced. This software allows for the automation of various manufacturing processes, such as die design, die making, and machining, which results in higher precision and faster production. It also enables real-time monitoring of the forging process, allowing for quick adjustments to ensure optimal results. Simulation tools have also played a crucial role in advancing forging processes. With the help of simulation software, manufacturers can simulate the entire forging process virtually, predicting and optimizing various parameters such as temperature, pressure, and material flow. This allows for the identification and resolution of potential issues before the actual forging process, reducing the risk of defects and improving the overall product quality. The implementation of these technological advancements has resulted in reduced lead times, as the design and manufacturing processes are streamlined and optimized. Improved product quality is achieved through precise design and simulation, minimizing defects and ensuring consistent performance of forgings. Additionally, increased productivity is realized through automation and real-time monitoring, allowing for faster production and better resource utilization.
COVID-19 IMPACT
Pandemic has caused disruptions in demand and supply chains, while also highlighting the importance of sustainability and supply chain resilience in the market
During the initial phase of the pandemic, widespread lockdowns, travel restrictions, and supply chain disruptions resulted in decreased demand across various end-use industries such as automotive, aerospace, and industrial equipment. Many manufacturing facilities were temporarily shut down, leading to a decline in production and sales. The pandemic has also accelerated certain trends that have long-term implications for the market. For example, the growing focus on sustainability and environmental concerns has gained further momentum during the pandemic, leading to increased demand for lightweight materials, which are known for their high strength-to-weight ratio and potential for reducing carbon emissions. The pandemic has highlighted the importance of supply chain resilience and localized manufacturing, leading to a shift towards regionalization of supply chains and localized production of critical components, to mitigate risks associated with global disruptions. The impact of COVID-19 on the market has been multifaceted, with short-term disruptions and long-term changes driven by evolving demand patterns, supply chain dynamics, and industry trends. The full extent of the impact will continue to unfold as the global economy recovers from the pandemic and adjusts to the new normal.
LATEST TRENDS
Demand is expected to grow, driven by the increasing adoption of advanced aluminum alloys in various applications
Aluminum alloys are preferred for forging applications due to their favorable properties, such as high strength, good corrosion resistance, and excellent machinability. These properties make aluminum alloys suitable for a wide range of applications in industries such as aerospace, automotive, electrical, and engineering machinery. High-strength aluminum alloys offer an improved strength-to-weight ratio, making them ideal for applications where lightweight materials with high strength are required, such as in the aerospace and automotive industries. Aluminum-lithium alloys, on the other hand, offer even higher strength and stiffness compared to traditional aluminum alloys, making them highly desirable for applications where weight reduction is critical, such as in aerospace and military applications. The adoption of advanced aluminum alloys in various applications is expected to drive the demand. Forging is a preferred manufacturing process for aluminum alloys as it allows for the creation of complex shapes and precise dimensions, while also improving the mechanical properties of the material. They offer superior strength, durability, and reliability, making them highly suitable for critical applications where performance and safety are paramount.
ALUMINUM FORGINGS MARKET SEGMENTATION
By Type Analysis
According to type, the market can be segmented into conventional aluminum forgings, custom aluminum forgings. Conventional aluminum is the leading type segmentation.
By Application Analysis
Based on application, the market can be divided into automotive, aerospace & military, electrical industry, engineering machinery, general industrial machinery. Aerospace & military is the leading application segmentation.
DRIVING FACTORS
Emphasis on light weighting in the automotive and aerospace industries is driving demand, as they offer a high strength-to-weight ratio
The growing emphasis on light weighting in the automotive and aerospace industries is driving the market growth. Both industries are seeking ways to improve fuel efficiency, reduce emissions, and enhance the overall performance of their products, and lightweight is a key strategy to achieve these goals. They are ideal for lightweight applications due to their high strength-to-weight ratio, which allows for the creation of lightweight yet strong components. In the automotive industry, lightweight is a critical factor for improving fuel economy and reducing emissions. By using lightweight materials, automakers can reduce the weight of vehicles, which in turn reduces the energy required to propel them. This leads to improved fuel efficiency and reduced greenhouse gas emissions. They are used in various automotive components, such as engine parts, transmission components, suspension systems, and chassis components, to achieve weight reduction without compromising on strength and durability. The growing emphasis on light weighting in the automotive and aerospace industries is driving the demand as manufacturers seek lightweight yet strong components to improve the performance and efficiency of their products. This trend is expected to continue driving the market growth as automotive and aerospace industries continue to prioritize light weighting as a key strategy to achieve their sustainability and performance goals.
Increasing focus on renewable energy in the wind and solar power sectors is driving the demand for the manufacturing of wind turbines
The growing focus on renewable energy, particularly in the wind and solar power sectors, is driving the demand in the market. They are used in the manufacturing of various components in wind turbines, such as hubs, blades, and gearbox housings, due to their lightweight and high-strength properties. With the increasing global adoption of renewable energy sources to reduce carbon emissions and promote sustainable energy production, the demand for wind turbines has been steadily growing. Wind turbines require lightweight and durable components to optimize performance and efficiency. Their high strength-to-weight ratio provides an ideal solution for these requirements. They offer excellent corrosion resistance, which is crucial for wind turbines installed in harsh environments. The growing focus on renewable energy, particularly in the wind and solar power sectors, is driving the demand as a key component in wind turbine manufacturing, thereby contributing to the overall aluminum forgings market growth.
RESTRAINING FACTORS
Volatility in aluminum prices can impact the cost of raw materials, leading to potential impacts on pricing, profitability, and overall market demand
The prices of aluminum, like any other commodity, are influenced by various factors such as global supply and demand dynamics, economic conditions, and trade policies. For example, changes in global aluminum production, demand from key industries, and geopolitical factors can impact aluminum prices. When aluminum prices experience volatility, it can have a direct impact on the cost of raw materials used in the production. As aluminum is a key material in the manufacturing of forgings, fluctuations in its prices can affect the overall cost structure of producing forgings. During periods of high aluminum prices, the cost of raw materials may increase, leading to higher production costs and reduced profitability for manufacturers. This may result in higher prices for finished forgings, which could impact their competitiveness in the market or reduce demand from customers. On the other hand, during periods of low aluminum prices, manufacturers may benefit from lower raw material costs, potentially leading to increased profitability and competitiveness in the market.
-
Request a Free sample to learn more about this report
ALUMINUM FORGINGS MARKET REGIONAL INSIGHTS
Asia-Pacific emerges as the leading region in the market, driven by robust industrialization, and manufacturing capabilities, resulting in a high market share and a fast growth rate
The Asia-Pacific region is considered the leading region in the global market. The region not only holds a significant aluminum forgings market share but is also expected to witness the fastest growth rate in the coming years. Several factors contribute to the dominant position of Asia-Pacific in the market. The region is home to major emerging economies such as China and India, which are witnessing rapid industrialization and urbanization. This is driving the demand in various sectors, including automotive, aerospace, construction, and consumer goods. It is a hub for manufacturing activities, with a large number of aluminum forging manufacturers and suppliers based in countries like China, Japan, and India. These manufacturers are leveraging cost-effective production capabilities and technological advancements to meet the growing demand in the region and globally. The growing automotive industry in Asia-Pacific, driven by rising disposable incomes, urbanization, and changing consumer preferences, is also a key factor propelling the demand. Lightweight and high-strength forgings are increasingly being used in automotive components to improve fuel efficiency and reduce emissions, aligning with the region's strict emission norms and regulations.
KEY INDUSTRY PLAYERS
Market players' emphasis on innovation, sustainability, customer relationships, global expansion, and operational efficiency drives competitiveness
Key market players in the industry employ various strategies to maintain their competitiveness and drive growth. These strategies include a focus on innovation and research and development (R&D) to develop advanced aluminum forging technologies and solutions. Sustainability and environmental stewardship are also emphasized, with efforts to reduce the environmental impact of operations. Global expansion through strategic acquisitions and partnerships, as well as product differentiation by offering customized solutions to meet customer requirements, is another common strategy. Customer relationships are prioritized, with an emphasis on providing technical support and enhancing customer satisfaction. Operational efficiency and cost optimization are also key focus areas to maintain competitiveness. Additionally, diversifying product offerings and expanding into emerging markets are part of the strategies employed by some market players. Quality and reliability are prioritized to maintain customer loyalty. These strategies are aimed at driving market growth and maintaining a leading position in the industry.
List of Top Aluminum Forgings Companies
- Aluminum Precision Products (US)
- Dynacast International (APAC)
- Continental Forge Company (US)
- Queen City Forging (US)
- Sun Fast International (US)
- Consolidated Industries (US)
- Anderson Shumaker (US)
REPORT COVERAGE
This research profiles a report with extensive studies that take into description the firms that exist in the market affecting the forecasting period. With detailed studies done, it also offers a comprehensive analysis by inspecting the factors like segmentation, opportunities, industrial developments, trends, growth, size, share, restraints, etc. This analysis is subject to alteration if the key players and probable analysis of market dynamics change.
Attributes | Details |
---|---|
Market Size Value In |
US$ 88.15 Billion in 2024 |
Market Size Value By |
US$ 150 Billion by 2033 |
Growth Rate |
CAGR of 6.08% from 2025 to 2033 |
Forecast Period |
2025-2033 |
Base Year |
2024 |
Historical Data Available |
Yes |
Regional Scope |
Global |
Segments Covered |
|
By Type
|
|
By Application
|
FAQs
The global aluminum forgings market is expected to USD 150 billion by 2033.
The aluminum forgings market is expected to exhibit a CAGR of 6.08% over forecast period.
Emphasis on light weighting in the automotive and aerospace industries is driving demand, as they offer a high strength-to-weight ratio.
Aluminum Precision Products, Dynacast International, Continental Forge Company, Queen City Forging are the top companies operating in the aluminum forgings market.