What is included in this Sample?
- * Market Segmentation
- * Key Findings
- * Research Scope
- * Table of Content
- * Report Structure
- * Report Methodology
Download FREE Sample Report
Carbon Fiber in Automotive Market Size, Share, Growth, and Industry Analysis, By Type (Sheet Molding Compound, Short Fiber Thermoplastic (SFT), Long Fiber Thermoplastic (LFT), Prepreg and Others), By Downstream Industry (Passenger Car and Commercial Vehicle), and Regional Forecast to 2033
Trending Insights
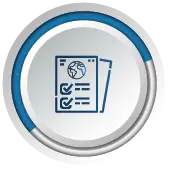
Global Leaders in Strategy and Innovation Rely on Our Expertise to Seize Growth Opportunities
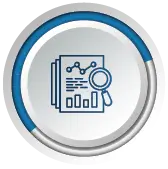
Our Research is the Cornerstone of 1000 Firms to Stay in the Lead
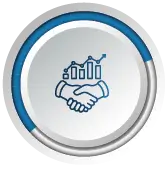
1000 Top Companies Partner with Us to Explore Fresh Revenue Channels
CARBON FIBER IN AUTOMOTIVE MARKET OVERVIEW
The global Carbon Fiber in Automotive Market size stood at USD 0.924 billion in 2024 and is projected to reach USD 0.971 billion in 2025, growing further to USD 1.446 billion by 2033 at an estimated CAGR of 5.1% from 2025 to 2033.
Carbon fiber plays an important role in automotive engineering because it is a special composite made by forming Carbon-Fiber-Reinforced Plastic (CFRP) tightly bonded in a plastic matrix. It is five times lighter than steel and offers the same or higher strength which means cars get better gas mileage, accelerate faster, brake more effectively and handle better. Its ability to stay strong under pressure and resist decay over time makes it well suited for crash structures. Its stability across a wide range of temperatures means they can design planes with more details and smooth lines than they could with metals. Its trademark woven finish gives luxury and sporty vehicles a premium and stylish appearance.
Carbon fiber can be found in several areas, including vehicle bodies, main structural components, wheels, drive shafts and battery boxes for electric cars. The strength and weight-reducing quality of magnesium are used in interior trim and brakes in performance cars. Organic polymer threads such as polyacrylonitrile (PAN) are first spun and then strengthened and carbonized by applying high heat. With surface treatments, resin sticks better to the fabric. Simple wet lay-up, as well as prepreg lamination and resin transfer molding, help to set the fiber shapes. This process helps produce precise parts that offer outstanding performance, efficiency and reliability.
COVID-19 IMPACT
Pandemic disrupted supply chains, delayed production and severely affected the market
The global COVID-19 pandemic has been unprecedented and staggering, with the market experiencing lower-than-anticipated demand across all regions compared to pre-pandemic levels. The sudden market growth reflected by the rise in CAGR is attributable to the market’s growth and demand returning to pre-pandemic levels.
The pandemic has caused major difficulties in the carbon fiber supply chain for the automotive industry. Since global imports and exports were almost shut down, manufacturers struggled to receive both raw and finished CFRP components on time. The industry’s heavy connection to Japan, a significant carbon fiber producer, made the situation worse. Consequently, auto factories struggled with supply delays, ceased production and spent more, slowing the introduction of new materials in future models. This exposed a significant weakness in the industry’s strategy for sourcing supplies around the world.
LATEST TRENDS
Growing emphasis on sustainability and recycling to drive the market
A focus on sustainability is leading to significant progress in making carbon fiber for automotives. Using recycled carbon fibers made from scrap or unwanted materials allows companies to decrease their environmental footprint and improve resource efficiency. Experts are discovering that using lignin and cellulose instead of chemicals derived from oil is both possible and beneficial. Various technologies are being designed to reduce emissions that occur during the high-temperature processes. These improvements are designed to lower the carbon footprint of carbon fiber without decreasing its usefulness. The rising demand for environmental solutions is making sustainable carbon fiber necessary for the future of efficient and lightweight vehicles.
CARBON FIBER IN AUTOMOTIVE MARKET SEGMENTATION
BY TYPE
Based on type, the global market can be categorized into Sheet Molding Compound, Short Fiber Thermoplastic (SFT), Long Fiber Thermoplastic (LFT), Prepreg and Others
-
Sheet Molding Compound: Sheet Molding Compound (SMC) is a type of composite that uses chopped carbon fibers and a thermosetting resin binder which is then formed into sheets. It makes it possible to build complex and lightweight car components quickly and in large quantities. The spreading of fibers in all directions enables smooth printing and supports detailed patterns. The materials used in SMC are known for their power, solidity and endurance. Its use for the frame and outside panels is rising because it is both effective and affordable.
-
Short Fiber Thermoplastic (SFT): Short Fiber Thermoplastic (SFT) uses carbon fibers that are quite short and mixes them with a thermoplastic, making them easier to work with and recycle. They are molded by injection for quickly making large numbers of auto parts. These parts offer fair strength and rigidity and thus, are used for components that do not require a lot of strength. In the automotive industry, composites can be found in both the cabin and the engine compartment. Being re-melted makes it easier to promote environmental sustainability in auto-making.
-
Long Fiber Thermoplastic (LFT): Long Fiber Thermoplastic (LFT) composites use longer carbon fibers combined with thermoplastic resin which helps the materials resist both strength and impacts. They provide better load transfer than short fiber thermoplastics. LFTs play a key role in the production of demanding automotive parts that must be both tough and light. Both injection and compression methods are commonly used to shape these composites. Common applications include front-end modules and seat structures.
-
Prepreg: Prepreg contains carbon fiber material already soaked with a partially cured resin, allowing for precise alignment of the fibers and easier management of the resin. It results in parts that have strong, firm construction and an excellent finish. Since weight is crucial for sporty and luxury models, auto manufacturers rely on prepregs for their designs. Tissues are processed in a slower and more expensive method using an autoclave or oven to achieve superior quality. Usually, carbon fiber is found in various vehicle parts, including body panels, chassis sections and racing equipment.
-
Others: Others type of material is continuous fiber-reinforced thermoplastics, hybrid composites and advanced molding compounds. For vital structural elements, continuous fibers offer exceptional mechanical features. Carbon is combined with either glass or aramid fibers in hybrid composites to keep them affordable and excellent at standing up to force. Customized architectures or resins are used in novel compounds for special requirements in the automotive industry. These materials serve niche or next-generation applications requiring unique strength, durability and lightweight properties.
BY APPLICATION
Based on downstream industry, the global market can be categorized into Passenger Car and Commercial Vehicle
-
Passenger Car: Passenger car use carbon fiber focus on enhancing performance, efficiency and safety. Lightweight construction improves acceleration, handling and reduces emissions. Automotive use it in body panels, roofs, chassis and EV passenger cells for strength and protection. Its stiffness enables innovative, ergonomic designs in modern cars. As costs drop, carbon fiber is expanding beyond luxury into mainstream models.
-
Commercial Vehicle: Commercial Vehicle use carbon fiber focuses on reducing weight to boost payload and efficiency. It enhances durability and fuel economy in trucks, buses and delivery vans. Lighter builds support lower emissions and sustainability goals. Carbon fiber’s corrosion and fatigue resistance suits demanding commercial use. Its role is growing as logistics shift toward greener and next-generation designs.
MARKET DYNAMICS
Market dynamics include driving and restraining factors, opportunities and challenges stating the market conditions.
DRIVING FACTORS
Growth of Electric Vehicles (EVs) to boost the market
The rise in EVs is boosting to increase carbon fiber in automotive market growth. Since EV manufacturers are focused on reducing vehicle weight to extend battery range and improve overall efficiency of carbon fiber’s exceptional strength-to-weight ratio becomes a vital asset. The use of carbon fiber in structural components, battery enclosures and body panels helps EVs improve on performance, safety and energy efficiency. This material reduces the bulk of heavy batteries without negatively impacting the durability or crash safety of the vehicle. With more electric cars being created, automakers are investing more in carbon fiber components. Lighter and more efficient EVs made possible by such materials highlight the importance of this approach for the future of cars.
Stringent environmental and regulatory requirements to expand the market
Stringent rules set for environmental standards are helping more automakers turn to carbon fiber. Strict emissions laws are being enforced and authorities are working to develop greener mobility solutions. Automakers are using more carbon fiber and other lightweight materials to make their cars lighter, leading to less fuel and CO₂ emissions to fulfill the standards. Being both strong and stiff, this material supports lasting safety and helps reduce environmental impact. With the rules becoming stricter, it is becoming more important for the automotive industry to use carbon fiber and lighten the weight of their vehicles.
RESTRAINING FACTOR
High production cost to potentially impede the market
A major challenge of carbon fiber in automotive is the high cost of producing it. Carbon fiber is manufactured in more energy-intensive ways than steel or aluminum and involves important processes such as stabilizing, carbonizing and molding accurately. Using raw materials such as PAN adds to the large cost of producing this fiber. As a result, only high-end, performance-oriented or limited vehicles can afford to use the material due to its expensive nature. Wide scale transformation in the industry is delayed for mainstream manufacturers due to the high cost involved. Carbon fiber will become popular in the automotive industry if production costs are reduced through automating the process, finding new materials and recycling when possible.
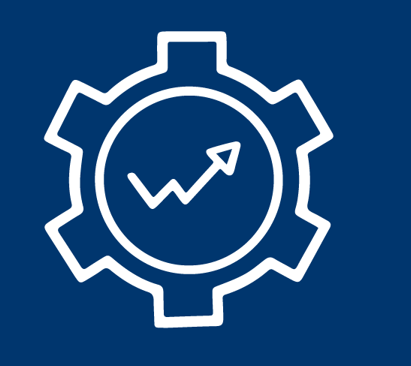
Integration into structural and safety components to create opportunity for the market
Opportunity
Integration carbon fiber in vehicles’ structure and safety parts is shaping the future of automobile engineering by making vehicles stronger and lighter. By having superior strength-to-weight ratios, manufacturers can strengthen chassis, roof areas, side zones and front-end structures without excessive weight gain. This reduces the risk of injury to passengers and helps keep the structure intact. The rigid structure of carbon fiber makes vehicles more durable and allows drivers to handle them precisely, enhancing performance and lifespan. As a result, the material can be formed into unique designs that enhance aerodynamics and ergonomics. With greater safety and efficiency required by regulations, carbon fiber is now essential for vehicles that meet the expectations of modern design. To developing vehicles that meet both structural performance and safety benchmarks in modern automotive design.
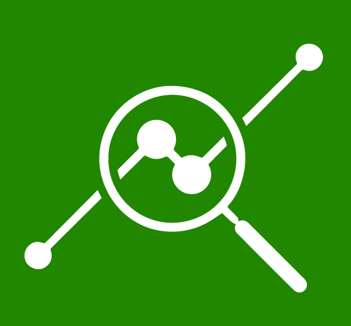
Environmental and sustainability concerns to challenge the market
Challenge
The use of carbon fiber in cars is limited because of issues related to the environment and sustainability. Creating this product requires a great deal of energy, often using PAN which is made from oil and therefore adds to carbon emissions. Also, large amounts of waste, including usable leftover materials, are created during manufacturing. Unlike ordinary metals, carbon fiber composites are not practical to recycle because routine methods can damage the fibers and limit their use in demanding applications. It makes it harder to manage old cars and raises questions about the harm they will cause in the future. Addressing these issues is essential for aligning carbon fiber use with evolving automotive sustainability goals.
-
Request a Free sample to learn more about this report
CARBON FIBER IN AUTOMOTIVE MARKET REGIONAL INSIGHTS
-
NORTH AMERICA
North America’s carbon fiber in automotive market growing mainly because of the United States’ efforts in research and development, tough fuel guidelines and surging demand for light materials. With more electric vehicles being used in the region, carbon fiber technology helps improve the batteries for better range and efficiency. Additionally, expertise from the aerospace and defense industries help improve carbon fiber production, making it available for use in more cars than only luxury cars.
-
EUROPE
The Europe market is leading in carbon fiber in automotive market share because of its well-developed automotive and aerospace businesses. Companies in this region use carbon fiber to ensure their products have a fine design and perform well. Stricter EU rules on emissions encourage manufacturers to switch to lighter building materials to achieve their CO₂ goals, leading to greater demand. Moreover, Europe’s dedication to green practices, innovative ideas and quality manufacturing supports sustained growth in carbon fiber. The presence of well-organized supply chains and proactive government policies strengthen Europe’s leading position in the automotive carbon fiber market.
-
ASIA
The Asia Pacific region leads in the growth of automotive carbon fiber due to the high level of automotive production in China, Japan, South Korea and India. The efforts of government and its regulations encourage the use of lightweight and electric cars. More people buying luxury cars encourage the use of carbon fiber, making it available to more clients as costs to produce the material fall. The rise of EVs and new technology is making Asia Pacific a leading player in the future of automotive carbon fiber.
KEY INDUSTRY PLAYERS
Key industry players are investing in research and development for market expansion
Key industry players are investing in research and development to improve carbon fiber technologies and their application in automotives. These investments work on making superior resin systems to make products more robust, effective and lighter. Firms are adjusting the properties of fibers, making them stronger and more flexible to help the automotive industry. There are also initiatives designed to enhance composite structures, allowing for better and more effective use in vehicles. By achieving these goals, the industry hopes to make carbon fiber more practical for large-scale use, resulting in better fuel efficiency, safety and cleaner energy in vehicles.
LIST OF TOP CARBON FIBER IN AUTOMOTIVE COMPANIES
- Hexcel (U.S.)
- Axon (U.K.)
- Cytec Solvay Group (Belgium)
- Zoltek (U.S.)
- Sigmatex (U.K.)
- DOWAKSA (Turkey)
- Hyosung Corporation (South Korea)
- Formosa Plastic (Taiwan)
- Plasan Carbon Composites (Israel)
- GURIT (Switzerland)
- Toray (Japan)
- Rivers Carbon Technologies (U.S.)
- SGL (Germany)
KEY INDUSTRY DEVELOPMENT
April 2025: Solvay has partnered with Cavalinho to cut CO₂ emissions from transportation in Brazil by 90% by 2030 through a fleet of 60 biofuel-powered trucks. Launching in 2026 at its Paulínia site, the initiative supports Solvay’s goal to reduce scope 3 emissions by 20%. Combined with its biomass boiler project, CO₂ reductions at Paulínia will reach 97% by 2027.
REPORT COVERAGE
The study encompasses a comprehensive SWOT analysis and provides insights into future developments within the market. It examines various factors that contribute to the growth of the market, exploring a wide range of market categories and potential applications that may impact its trajectory in the coming years. The analysis takes into account both current trends and historical turning points, providing a holistic understanding of the market's components and identifying potential areas for growth.
Carbon fiber in automotive is transforming vehicle design by offering superior strength-to-weight advantages, enabling improved performance, fuel efficiency, and safety. Its use spans body panels, battery enclosures, chassis, and interior components, especially in electric and luxury vehicles. Despite high production costs and recycling challenges, its adoption is driven by strict emission norms, growing EV demand, and structural benefits. Advancements in recycled fibers, sustainable feedstocks, and molding technologies are further boosting market potential. Regional growth is strong in North America, Europe, and Asia Pacific. With key players investing in research and development, carbon fiber is essential to the automotive industry’s shift toward lightweight, sustainable innovation.
Attributes | Details |
---|---|
Market Size Value In |
US$ 0.924 Billion in 2024 |
Market Size Value By |
US$ 0.971 Billion by 2033 |
Growth Rate |
CAGR of 1.446% from 2025 to 2033 |
Forecast Period |
2025-2033 |
Base Year |
2024 |
Historical Data Available |
Yes |
Regional Scope |
Global |
Segments Covered |
|
By Types
|
|
By Applications
|
FAQs
The Carbon Fiber in Automotive Market is expected to reach USD 1.446 billion by 2033.
The Carbon Fiber in Automotive Market is expected to exhibit a CAGR of 5.1% by 2033.
Growth of Electric Vehicles (EVs) and stringent environmental and regulatory requirements are some of the driving factors in the market.
The key market segmentation, which includes, based on type, the carbon fiber in automotive market is Sheet Molding Compound, Short Fiber Thermoplastic (SFT), Long Fiber Thermoplastic (LFT), Prepreg and Others. Based on application, the carbon fiber in automotive market is classified as Passenger Car and Commercial Vehicle.