What is included in this Sample?
- * Market Segmentation
- * Key Findings
- * Research Scope
- * Table of Content
- * Report Structure
- * Report Methodology
Download FREE Sample Report
Casting and Forging Market Size, Share, Growth, and Industry Analysis, By Type (Closed Die Forging, Open Die Forging), By Application (Automobile, Aerospace, Mining, Construction, Industrial, Others) and Regional Forecast to 2033
Trending Insights
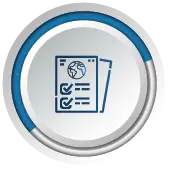
Global Leaders in Strategy and Innovation Rely on Our Expertise to Seize Growth Opportunities
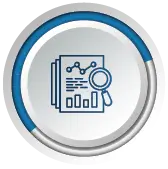
Our Research is the Cornerstone of 1000 Firms to Stay in the Lead
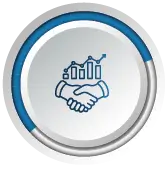
1000 Top Companies Partner with Us to Explore Fresh Revenue Channels
CASTING AND FORGING MARKET OVERVIEW
The global Casting and Forging Market Market was valued at approximately USD 180 billion in 2024 and is projected to reach USD 187.38 billion in 2025, further expanding to USD 260 billion by 2033, growing at a CAGR of about 4.1% from 2025 to 2033.
The industry relies on the casting and forging market to supply important parts used in automotive, aerospace, construction, mining, oil & gas and heavy machinery. You mix metal and pour it into a mold so it forms the shape you need, making it suitable for complicated shapes in large quantities. Unlike welding, forging gives metal extra strength, endurance and structure by compacting it which is important when design strength matters most. A constant rise in demand for light materials, strong parts and precise designs is bringing steady growth to the market. Machines that make items by simulating, printing in 3D and pressing in automated presses are making production more efficient and improving products. In the market, Asia-Pacific is at the top for both production and consumption, supported by strong manufacturing and infrastructure growth in North America and Europe. These new regulations are promoting industry’s shift to cleaner sources of energy. There is strong competition and fragmentation among casting and forging companies, who are using mergers, improving their technology and raising their production capacities to succeed further. Growing demand for cars that run on electricity, aerospace parts and systems that use renewable energy is helping the market to increase.
COVID-19 IMPACT
Casting and Forging Market Had a Negative Effect Due to Supply Chain Disruption During COVID-19 Pandemic
The global COVID-19 pandemic has been unprecedented and staggering, with the market experiencing lower-than-anticipated demand across all regions compared to pre-pandemic levels. The sudden market growth reflected by the rise in CAGR is attributable to the market’s growth and demand returning to pre-pandemic levels.
Initially, the Casting and Forging Market share was heavily hit because of global supply chain disruptions, not enough workers and temporary plant shutdowns because of COVID-19. Restrictions surrounding lockdowns and travel reduced the number of customers wanting luxury cosmetics and specific industry goods which decreased co-packing quantities. Because of the new health and safety rules, many co-packers struggled to stay compliant which slowed operations and created extra costs for them. Particularly those co-packing agreements linked to moving goods between nations were put off or ended over transport delays. For smaller and medium-sized co-packers, handling money wisely and keeping up with fast changes in demand became a big problem. Additionally, it was difficult for co-packers to plan, because brand owners could not reliably predict what would be sold. Problems with packaging supplies and logistics slowed down the process. Although food and pharmaceutical companies still needed packaging, the clamor for co-packing services lessened across the industry in the early stages of the pandemic. By the end of 2021, businesses adjusted to the new situation by using updated agility and digital systems in their supply chains which led to resilience and growth afterwards.
LATEST TREND
Organic and Clean-Label Infant Nutrition Drive Market Growth
The casting and forging market is moving towards greater precision, as innovations in these technologies result in higher demand for precise parts. Automobile, aerospace and medical device sectors now require components that are more accurate, have complex shapes and are made from stronger materials. As a result, more manufacturers are choosing simulation-driven die design, near-net shape forging and investment casting to minimize the amount of material they process. In addition, using CAD, instant quality control and robotics in production helps increase the reliability and repeatability of products. The use of 3D sand printing and vacuum casting in casting permits higher flexibility in design and shortens the time needed to create prototypes. Using automated hammer presses and servo-hydraulic presses is making forging faster and freeing workers from repetitive work. They enhance how well components work and how long they last and they benefit the environment by decreasing both waste and energy use. Since users of electric vehicles and aerospace engines seek better performance, lighter components and reliability, casting and forging businesses are putting precision manufacturing at the heart of their competitiveness. We should see this increase as companies implement newer, digitally connected and more efficient manufacturing methods.
CASTING AND FORGING MARKET SEGMENTATION
By Type
Based on type, the global market can be categorized into Closed Die Forging, Open Die Forging
- Closed Die Forging: As impression-die forging, it employs enclosing dies so that components with many complexities and high strength can be manufactured with exact tolerances. Optimized for automotive and aerospace businesses.
- Open Die Forging: Includes changing metal shape with flat or basic dies that do not touch the whole piece. It works best for creating big parts that need to be tough mechanically, for example shafts and rings.
By Application
Based on application, the global market can be categorized into Automobile, Aerospace, Mining, Construction, Industrial, Others
- Automobile: When making engine blocks, components for transmissions and suspension parts, casting and forging are important because they must be strong, can withstand repeated use and be prepared at a good cost.
- Aerospace: Forging enables the making of both strong and light landing gear and turbine disk parts. For the strongest airframe components, casting is required. Mining: Hard, durable equipment for tough environments such as tools, replaceable parts and supports, is made through forging and casting.
- Construction: VOC vehicles have gears, frames and structural connectors made through forging and casting to sustain harsh situations.
- Industrial: Couplings, rollers and valves which are common to the machinery sector, are made through casting and forging to ensure high-performance and customization.
- Others: Both methods are used in shipbuilding, oil and gas and defense, helping to make tough and corrosion-resistant parts.
MARKET DYNAMICS
Market dynamics include driving and restraining factors, opportunities and challenges stating the market conditions.
Driving Factors
Growing Demand from Automotive and Aerospace Sectors Boost the Market
The demand from the automotive and aerospace sectors is largely powering the casting and forging market growth. High strength and fatigue resistance in crankshafts, camshafts, gears and suspension parts in automobiles are provided most effectively through forging and precision casting. As car manufacturers build more electric vehicles and produce more cars, they are choosing lightweight forged aluminum and cast magnesium parts to help increase efficiency. The requirement for aircraft to be lightweight, strong and able to resist high temperatures has made forged turbine disks, fan blades and precision-cast airframe parts very popular in aerospace. Booming commercial and military aviation along with the rise of aircraft deliveries after COVID-19 are speeding market growth. Since they demand top quality, these industries have come up with new ways to forge and cast metals, always needing advanced, efficient metals.
Technological Advancements in Casting and Forging Processes Expand the Market
Because new types of casting and forging help make products more efficient, accurate and better, markets are expanding as a result. Near-net shape forging, vacuum casting and investment casting all allow for less waste and are often efficient with the use of tools. Greater use of simulation and process monitoring helps catch more defects and cut back on rework. Products are produced more quickly and with better consistency thanks to automation and robotics which also lower the need for workers. Making casting molds and tooling using 3D printing has cut the development process and made it easier to model complex shapes. Using servo-hydraulic presses and isothermal forging, it is now possible to control metal flow and the appearance of internal grains with greater accuracy. This new technology improves how things are done and helps tackle sustainability by cutting down on usage and emissions. In trying to reduce costs while improving performance, manufacturers rely increasingly on new casting and forging technologies which are important to defense, aerospace and renewable energy sectors.
Restraining Factor
High Energy Consumption and Emission Regulations Potentially Impede Market Growth
One of the primary restraints in the casting and forging marketplace is the high power depth of manufacturing tactics, coupled with stringent environmental policies. Both strategies require extensive thermal and mechanical power, especially for the duration of melting, heating, and deformation levels, which contributes to excessive greenhouse gas emissions. Compliance with global emission norms and the rush for carbon neutrality have increased operational prices for producers, particularly in areas with strict environmental policies such as Europe and North America. Additionally, the dependence on non-renewable electricity assets and old machinery in many foundries in addition exacerbates the issue. Regulatory frameworks such as the EU Emissions Trading System (ETS) and carbon taxation in several countries are compelling agencies to spend money on purifier technology, increasing capital expenditure. While sustainable forging and casting techniques are emerging, their adoption remains restrained due to high initial prices, slowing down the marketplace’s capability, mainly for small and mid-sized firms.
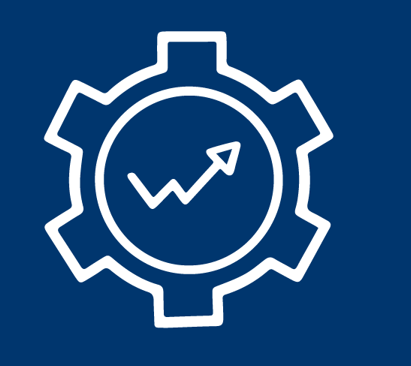
Electric Vehicles and Renewable Energy Components Creates Opportunity for The Product in The Market
Opportunity
The transition in the direction of electric automobiles (EVs) and renewable power structures provides vast opportunities for the casting and forging market. EVs require lightweight, high-electricity components along with electric motor housings, battery enclosures, and transmission structures that are perfectly suited for precision casting and forging. The global push for easy electricity has additionally brought about an increase in demand for wind turbine parts, solar panel frames, and hydroelectric additives, many of which involve cast and cast metals. These packages require advanced production techniques for sturdiness and overall performance in severe situations. Governments globally are imparting incentives and funding to scale up green power infrastructure, driving demand for specialized metallic additives. As OEMs and infrastructure builders are looking for reliable and price-effective production partners, casting and forging firms can leverage this trend using innovation in materials and approaches tailor-made to EVs and renewables. This shift represents a multi-billion-dollar possibility for marketplace players over the next decade.
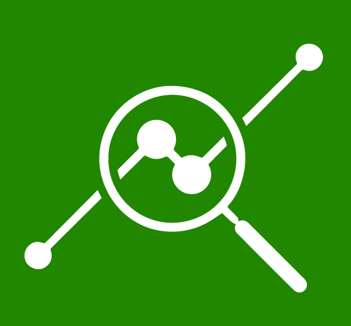
Skilled Labor Shortage and Workforce Aging Pose Could Be a Potential Challenge for Consumers
Challenge
A persistent challenge in the casting and forging market is the shortage of skilled personnel, compounded by an aging group of workers. Foundries and forging stores require technically gifted workers to deal with complicated machinery, fine control, and manner optimization. However, many professional employees are nearing retirement, and more youthful generations show restricted interest in getting into physically demanding, traditional production roles. The lack of vocational training applications and inadequate publicity of modernized manufacturing technologies further widens the skills gap. This scarcity can lead to production delays, first-rate inconsistencies, and multiplied education fees. Smaller companies, specifically, face trouble in attracting and retaining expertise, impacting their ability to scale operations. Automation and digitalization offer partial alleviation, however, the transition is gradual and capital-intensive. Addressing this mission will require industry-extensive efforts in group of workers development, schooling partnerships, and place of business modernization to make the world greater appealing to the next generation of employees.
-
Request a Free sample to learn more about this report
CASTING AND FORGING MARKET REGIONAL INSIGHTS
-
North America
North America performs a key function within the United States casting and forging market because of its superior production base and increasing investments in the defense, aerospace, and automobile sectors. The U.S., especially, houses predominant forging and casting corporations with high technological skills and innovation-focused production. The location is witnessing a call for from army vehicle and plane programs, due to the need for precision-solid and solid additives. Moreover, guidelines promoting infrastructure development and re-shoring of manufacturing are predicted to boost domestic metallic element production. The automobile industry’s shift towards electric-powered cars has also expanded the need for lightweight forged aluminum and cast magnesium parts. Strong compliance with first-rate and environmental standards fosters procedure upgrades and sustainability improvements. While labor prices are excessive, the emphasis on automation and Industry 4. solutions helps maintain competitiveness. Overall, North America’s strategic business priorities and strong R&D skills make it a key contributor to the worldwide marketplace.
-
Europe
Europe is a chief contributor to the casting and forging market, supported by its sturdy emphasis on sustainability, engineering excellence, and environmental compliance. Countries like Germany, France, and Italy have long-established business production ecosystems, specifically in the automobile, aerospace, and heavy equipment sectors. The vicinity is mainly the transition to eco-friendly production with investments in energy-green furnaces, recyclable alloys, and coffee-emission forging techniques. EU policies additionally encourage the improvement of cleaner methods and digitized deliver chains. European manufacturers prioritize high-precision components and have adopted advanced simulation and exceptional manipulation technologies to preserve global competitiveness. Additionally, the aerospace region, with players like Airbus, drives the call for solid and cast parts in jet engines and structural assemblies. Despite high electricity and hard work prices, innovation and regulatory guidance assist in maintaining the place’s leadership. The presence of skilled labor, research establishments, and sustainability-driven regulations makes Europe a cornerstone in the global casting and forging enterprise.
-
Asia
Asia Pacific is the most important and fastest-growing area in the casting and forging marketplace, driven by way of speedy industrialization, infrastructure growth, and the presence of value-efficient manufacturing hubs. China, India, Japan, and South Korea lead in both production and intake of casted and solid components, offering key sectors, inclusive of automobile, production, mining, and power generation. The place benefits from ample uncooked cloth availability, lower labor costs, and expanding business automation talents. Governments in India and China are investing in heavy engineering, renewable power, and defense infrastructure, further boosting demand. Asia-Pacific also serves as an international export base due to its scale and delivery chain integration. Although a few manufacturers face environmental and regulatory compliance challenges, efforts to modernize centers and enforce innovative technology are underway. The presence of both multinational businesses and agile neighborhood players guarantees a dynamic and aggressive panorama. Asia-Pacific’s boom trajectory makes it the most influential region in shaping the future of this marketplace.
KEY INDUSTRY PLAYERS
Key Industry Players Shaping the Market Through Innovation and Market Expansion
The global casting and forging market is rather competitive and capabilities a mixture of multinational groups and local players. Key players encompass Bharat Forge Limited (India), Thyssenkrupp AG (Germany), Arconic Corporation (USA), Nippon Steel Corporation (Japan), Aichi Steel Corporation (Japan), and Alcoa Corporation (USA). Bharat Forge is a worldwide leader in automobile and industrial forging, with a robust presence across Asia, Europe, and North America. Thyssenkrupp is known for its aerospace and heavy forging expertise. Arconic and Alcoa's recognition of precision casting and forging for aerospace and commercial programs. Aichi Steel, a Toyota Group employer, specializes in high-power automotive forgings. Other first-rate players include Precision Castparts Corp (USA), one of the biggest suppliers of aerospace castings, and Farinia Group (France), which operates multiple foundries and forging plants throughout Europe. These organizations are investing closely in automation, digitalization, and sustainability to enhance efficiency and stay aggressive. Mergers, strategic collaborations, and geographic enlargement are common strategies followed with the aid of these companies. The market additionally consists of several robust nearby businesses in China, India, and Southeast Asia, contributing notably to global output. As purchaser demands evolve, key players are those that specialize in offering lightweight, long-lasting, and precision-engineered answers.
List of Top Casting And Forging Market Companies
- Alcoa (U.S.)
- Schuler Group (Germany)
- Allegheny Technologies (U.S.)
- Aichi Steel (Japan)
KEY INDUSTRY DEVELOPMENT
March 2025: Bharat Forge Limited announced the inauguration of its new aluminum forging facility in Chakan, India, aimed at catering to electric vehicle and lightweight automotive component demand.
REPORT COVERAGE
The international casting and forging marketplace is poised for consistent boom, fueled by the increasing demand for high-energy, precision-engineered components throughout diverse industries. From automobile and aerospace to strength and heavy machinery, casting and forging serve as essential production techniques for producing durable and complicated metallic parts. Despite challenges including high energy consumption, professional hard work shortages, and unstable raw fabric fees, the market keeps adapting through technological innovation and procedure optimization. The adoption of automation, simulation software, and advanced alloys is improving high-quality, decreasing waste, and increasing productivity. Emerging opportunities in electric cars, renewable electricity, and protection production are expected to noticeably boost demand, particularly for lightweight and corrosion-resistant substances. Regional dynamics similarly form the market, with Asia Pacific dominating manufacturing due to its cost advantages and developing business infrastructure, even as North America and Europe lead in innovation and sustainable practices. Key players are responding with strategic investments, potential expansions, and collaborative ventures to reinforce their worldwide footprint. Government guide for infrastructure and smooth electricity initiatives also contributes to long-time period marketplace resilience. As industries pass in the direction of smart production and environmentally responsible operations, the casting and forging zone is about to play a pivotal role in helping global commercial development, with a strong emphasis on high-quality, efficiency, and flexibility.
Attributes | Details |
---|---|
Market Size Value In |
US$ 180 Billion in 2024 |
Market Size Value By |
US$ 260 Billion by 2033 |
Growth Rate |
CAGR of 4.1% from 2025 to 2033 |
Forecast Period |
2025-2033 |
Base Year |
2024 |
Historical Data Available |
Yes |
Regional Scope |
Global |
Segments Covered |
|
By Type
|
|
By Application
|
FAQs
Asia is the prime area for the Casting and Forging Market.
Growing Demand from Automotive and Aerospace Sectors Boost the Market & Technological Advancements in Casting and Forging Processes Expand the Market
The key market segmentation, which includes, based on type, the Casting and Forging Market is Closed Die Forging, Open Die Forging. Based on by Application, the Casting and Forging Market is Automobile, Aerospace, Mining, Construction, Industrial, Others.
The Casting and Forging market is expected to reach USD 260 billion by 2033.
The Casting and Forging market is expected to exhibit a CAGR of 4.1% by 2033.