What is included in this Sample?
- * Market Segmentation
- * Key Findings
- * Research Scope
- * Table of Content
- * Report Structure
- * Report Methodology
Download FREE Sample Report
Ceramic Foundry Sand Market Size, Share, Growth, And Industry Analysis, By Type (Under 70 Mesh, 70-140 Mesh, above 200 Mesh), By Application (Resin-coated Sand, Cold Core Box Process, No Bake Process, Lost-foam Casting Process), Regional Forecast From 2025 To 2033
Trending Insights
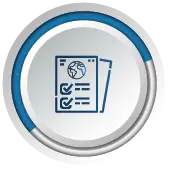
Global Leaders in Strategy and Innovation Rely on Our Expertise to Seize Growth Opportunities
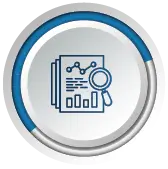
Our Research is the Cornerstone of 1000 Firms to Stay in the Lead
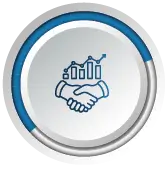
1000 Top Companies Partner with Us to Explore Fresh Revenue Channels
CERAMIC FOUNDRY SAND MARKET OVERVIEW
The global Ceramic Foundry SAnd Market size was USD 0.23 billion in 2024 and is expected to reach USD 0.44 billion by 2033, growing at a compound annual growth rate (CAGR) of about 7.6% during forecast period.
The global COVID-19 pandemic has been unprecedented and staggering, with the market experiencing lower-than-anticipated demand across all regions compared to pre-pandemic levels. The sudden rise in CAGR is attributable to the market's growth and demand returning to pre-pandemic levels once the pandemic is over.
Ceramic foundry sand, also known as Fused Ceramic Sand for Foundry or ceramite, refers to a type of sand used in foundry applications. It is produced by processing calcined bauxite through a series of steps, including melting, blowing, sieving, and blending. The main component of ceramic foundry sand is aluminum oxide (alumina). It is preferred over traditional silica sand in foundry processes due to its superior properties. It exhibits high refractoriness, meaning it can withstand high temperatures without melting or deforming. It also possesses stable inert characteristics, making it resistant to chemical reactions with molten metals. This stability ensures consistent performance in foundry applications. The spherical grain shape contributes to its excellent flowability, allowing it to easily fill intricate molds and cores. It also offers intrinsic hardness and wear resistance, which helps to extend the lifespan of molds and cores during the casting process. The use can result in improved casting quality, reduced defects, and enhanced dimensional accuracy in metal castings. It finds application in various foundry processes, including resin-coated sand, cold core box, no-bake, lost-foam casting, and others.
Ceramic foundry sand provides notable advantages compared to traditional silica sand in foundry applications. Its higher refractoriness, superior flowability, and improved dimensional accuracy contribute to enhanced casting quality and reduced defects. The higher refractoriness allows it to withstand high temperatures without melting or deforming, ensuring the integrity of the mold during the casting process. The superior flowability enables it to fill intricate molds and cores more effectively, reducing the risk of incomplete fillings and improving overall casting quality. Its improved dimensional accuracy helps achieve precise and consistent casting dimensions, resulting in better-fitting components and reduced rework. With manufacturers increasingly seeking higher-quality metal castings to meet industry demands, the demand has witnessed significant growth. Its advantages over silica sand make it a preferred choice for foundries looking to enhance casting performance and achieve superior product quality.
COVID-19 IMPACT
Pandemic caused disruption in supply chains and reduced demand for ceramic foundry sand
The COVID-19 pandemic has had a significant impact on the market. The outbreak and subsequent lockdown measures disrupted supply chains, leading to manufacturing and production delays. The temporary closure of foundries and reduced industrial activities hampered the demand. Travel restrictions and economic uncertainties affected the overall market growth. As industries gradually resumed operations and global economies started recovering, the demand began to pick up. The focus on infrastructure development, particularly in emerging economies, and the rebound of the automotive sector are expected to drive the market's recovery post-pandemic.
LATEST TRENDS
Growth of the foundry industry directly leads to an increased demand for ceramic foundry sand
The global foundry industry is experiencing growth due to industrialization, infrastructure development, and the rising demand for automobiles and consumer goods. They rely on high-performance materials to achieve improved casting outcomes. As the foundry industry expands, the demand increases proportionally. They seek to enhance their casting processes to meet the growing demand for high-quality metal castings, which drives the need for superior materials. Therefore, the growing foundry industry plays a direct role in driving the increased demand.
CERAMIC FOUNDRY SAND MARKET SEGMENTATION
By Type Analysis
According to type, the market can be segmented into under 70 mesh, 70-140 mesh, above 200 mesh.
By Application Analysis
Based on application, the market can be divided into resin-coated sand, cold core box process, no bake process, and lost-foam casting process.
DRIVING FACTORS
Increasing emphasis on casting efficiency has resulted in a rising demand
There is an increasing emphasis on casting efficiency in the foundry industry. With its superior flow ability and mold ability, it enables foundries to cast complex shapes and intricate designs with ease. This results in improved production efficiency and reduced time-consuming rework, leading to cost savings and higher productivity. As foundries strive to enhance their casting processes and achieve greater efficiency, the demand is increasing. The ceramic foundry sand market growth is due to the benefits it offers in terms of improved casting efficiency and overall operational effectiveness.
Shifting preference towards resin-coated sand due to several advantages
The preference for resin-coated sand in foundry applications is growing, and ceramic foundry sand plays a significant role in this segment. Resin-coating enhances the performance of the sand by improving its strength, and heat resistance, and reducing the emission of harmful gasses during the casting process. As foundries increasingly adopt resin-coated sand for its superior properties, the demand as a crucial ingredient is also on the rise. They offer several advantages, including better mold stability, improved dimensional accuracy, and reduced defects in castings. It provides enhanced flow ability, ensuring complex molds and intricate designs can be successfully cast. The resin-coating process also contributes to better mold strength, resulting in higher-quality castings. The increasing adoption of resin-coated sand by foundries is driven by the need for improved casting performance and higher-quality metal components. As a result, the demand, which serves as the base material for resin-coated sand, is experiencing substantial growth.
RESTRAINING FACTORS
Higher cost compared to silica sand causes limitations on its adoption in certain applications and industries
One of the restraining factors for the adoption of ceramic foundry sand is its relatively higher cost compared to traditional silica sand. The higher cost can pose limitations on its widespread adoption, particularly in industries or applications with strict budget constraints. Foundries and manufacturers may opt for more cost-effective alternatives, especially if the performance benefits are not deemed essential for their specific requirements. Despite the cost factor, the demand continues to grow in industries where its superior properties and performance advantages outweigh the cost considerations.
-
Request a Free sample to learn more about this report
CERAMIC FOUNDRY SAND MARKET REGIONAL INSIGHTS
Asia-Pacific emerges as the leading market driven by its dominance and strong growth potential in the region
Asia-Pacific is the leading region in the market, exhibiting significant growth and holding a substantial ceramic foundry sand market share. The region's dominance can be attributed to several factors such as the presence of major foundry industries, rapid industrialization, infrastructure development, and increasing demand for automobiles and consumer goods. Countries like China, Japan, and South Korea are major contributors to the growth of the market in the Asia-Pacific region. The region's robust manufacturing sector and focus on technological advancements are driving the demand for high-performance materials. As a result, the Asia-Pacific region is expected to continue its growth trajectory in the market.
KEY INDUSTRY PLAYERS
Key players' focus on growth strategies in the market leads to enhanced market position and increased customer satisfaction
Key players in the market are placing a significant focus on various aspects to maintain their market position and drive growth. These players are strategically emphasizing factors such as innovative trends and developments, expansion of product portfolios, mergers and acquisitions, collaborations, new product innovations, and geographical expansions. By implementing these growth strategies, companies aim to strengthen their competitive edge and cater to the evolving needs of customers. Key players are actively investing in research and development activities to introduce advanced technologies and improve the performance. This focus on continuous improvement and expansion enables them to meet the increasing demand and stay ahead in the market.
List of Top Ceramic Foundry Sand Companies
- Carbo Ceramics (North America)
- Itochu Ceratech (Asia)
- Kailin Foundry (Asia)
- Jingang New Materials (Asia)
- Sanmenxia Qiangxin (Asia)
- Henan Jinnaiyuan (Asia)
- CMP Group (North America)
REPORT COVERAGE
This research profiles a report with extensive studies that take into description the firms that exist in the market affecting the forecasting period. With detailed studies done, it also offers a comprehensive analysis by inspecting the factors like segmentation, opportunities, industrial developments, trends, growth, size, share, restraints, etc. This analysis is subject to alteration if the key players and probable analysis of market dynamics change.
Attributes | Details |
---|---|
Market Size Value In |
US$ 0.23 Billion in 2024 |
Market Size Value By |
US$ 0.44 Billion by 2033 |
Growth Rate |
CAGR of 7.6% from 2025 to 2033 |
Forecast Period |
2025-2033 |
Base Year |
2024 |
Historical Data Available |
Yes |
Regional Scope |
Global |
Segments Covered |
|
By Type
|
|
By Application
|
FAQs
The global ceramic foundry sand market is expected to touch USD 0.44 billion by 2033.
The ceramic foundry sand market is expected to exhibit a CAGR of 7.6% by 2033.
Increasing emphasis on casting efficiency has resulted in a rising demand.
Carbo Ceramics, Itochu Ceratech, Kailin Foundry, Jingang New Materials