What is included in this Sample?
- * Market Segmentation
- * Key Findings
- * Research Scope
- * Table of Content
- * Report Structure
- * Report Methodology
Download FREE Sample Report
Flux Coated Preforms Market Size, Share, Growth, and Industry Analysis, By Type (Leaded Flux Coated Preforms, Lead Free Flux Coated Preforms), By Application (Electronics, Semiconductor, Military & Aerospace, Medical, Others), Regional Insights and Forecast To 2032
Trending Insights
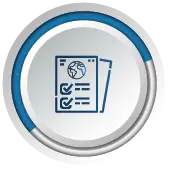
Global Leaders in Strategy and Innovation Rely on Our Expertise to Seize Growth Opportunities
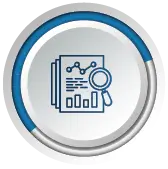
Our Research is the Cornerstone of 1000 Firms to Stay in the Lead
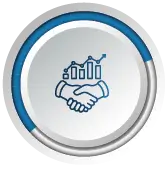
1000 Top Companies Partner with Us to Explore Fresh Revenue Channels
FLUX COATED PREFORMS MARKET OVERVIEW
global flux coated preforms market size was USD 0.1 billion in 2023 and market is projected to touch USD 0.16 billion by 2032 at CAGR 5.9% during the forecast period.
The flux-coated preforms market is experiencing a surge in demand as industries increasingly prioritize efficient soldering processes. These preforms, often made of metals like tin and lead, come coated with flux—a crucial element for promoting solder wetting and ensuring strong, reliable bonds. As electronic components become smaller and more complex, the need for precise and effective soldering solutions grows. Flux-coated preforms offer a convenient and controlled way to deliver flux during the soldering process, reducing defects and improving overall product quality. With the continuous evolution of electronics and manufacturing, the flux-coated preforms market is poised for sustained growth and innovation.
COVID-19 IMPACT
Market Growth Restrained by Pandemic Due to Supply Chain Disruptions
The global COVID-19 pandemic has been unprecedented and staggering, with the market experiencing lower-than-anticipated demand across all regions compared to pre-pandemic levels. The sudden market growth reflected by the rise in CAGR is attributable to market’s growth and demand returning to pre-pandemic levels.
The flux-coated preforms market faced significant challenges due to the negative impact of the COVID-19 pandemic. The global disruptions in supply chains, manufacturing slowdowns, and reduced consumer spending directly affected the electronics industry, a key consumer of flux-coated preforms. Lockdowns and restrictions impeded production and distribution, leading to delays and increased costs. Moreover, the economic uncertainty prompted many businesses to reevaluate their budgets, affecting investment in technology and manufacturing processes. Despite these setbacks, the market has shown resilience, adapting to new norms and leveraging innovations to navigate the challenges.
LATEST TRENDS
Innovative Integration Help Market Growth
Manufacturers are increasingly focusing on incorporating advanced technologies and materials into flux-coated preforms to enhance their performance and versatility. This trend aligns with the growing demand for precision in soldering processes, driven by evolving electronic component designs. From smart soldering alloys to improved flux formulations, the industry is embracing innovative solutions that not only streamline production but also contribute to higher quality solder joints. As technology continues to advance, the flux-coated preforms market's landscape is being reshaped by a commitment to cutting-edge integration.
FLUX COATED PREFORMS MARKET SEGMENTATION
By Type
Based on type the global market can be categorized into leaded flux coated preforms, lead free flux coated preforms.
Leaded flux-coated preforms, traditionally utilized in soldering processes, offer excellent wetting properties and ease of use. However, the industry is experiencing a notable shift towards lead-free alternatives due to environmental concerns and regulatory standards. Lead-free flux-coated preforms not only address these sustainability issues but also meet the evolving demands of the electronics industry. This categorization reflects the industry's commitment to providing diverse solutions, accommodating both traditional preferences and the growing need for eco-friendly and compliant soldering options.
By Application
Based on application the global market can be categorized into electronics, semiconductor, military & aerospace, medical, and others
The primary sectors include electronics, where flux-coated preforms play a crucial role in precise soldering for circuit boards and components. The semiconductor industry benefits from these preforms in intricate semiconductor device assembly. In the military and aerospace sector, flux-coated preforms ensure robust connections in mission-critical electronic systems. Moreover, the medical industry relies on these forms for assembling intricate medical devices. The others category encompasses various industries, showcasing the adaptability of flux-coated preforms across a spectrum of applications, highlighting their significance in ensuring reliable soldering in diverse technological realms.
DRIVING FACTORS
Miniaturization Demands Precision to Propels the Market
The relentless push toward miniaturization in electronic components is a primary driver propelling the flux-coated preforms market. As gadgets become smaller and more intricate, the need for precise soldering solutions intensifies. Flux-coated preforms play a pivotal role in ensuring accurate solder application, contributing to the manufacturing of compact yet high-performance electronic devices.
Rising Embrace of Renewable Energy Technologies to Steer the Market
The burgeoning renewable energy sector is another formidable force steering the flux-coated preforms market. With the increasing adoption of green technologies like solar panels and electric vehicles, the demand for robust and reliable soldering solutions has surged. Flux-coated preforms, with their ability to enhance solder joint quality, are integral to the production of sustainable energy systems, driving flux-coated preforms market growth amid the global shift towards cleaner energy sources.
RESTRAINING FACTOR
Environmental Concerns to Cast a Shadow on Flux-Coated Preforms
One significant restraining factor for the flux-coated preforms market is the growing scrutiny and concern regarding environmental impact. The traditional composition of flux-coated preforms often involves materials like lead, which raises apprehensions due to its environmental toxicity. Stringent regulations and increasing awareness about the ecological footprint of manufacturing processes have led to a shift towards environmentally friendly alternatives. As the industry navigates this challenge, innovations in eco-friendly flux formulations and sustainable manufacturing practices are crucial to overcoming environmental constraints and ensuring the continued growth of the flux-coated preforms market.
-
Request a Free sample to learn more about this report
FLUX COATED PERFORMS MARKET REGIONAL INSIGHTS
Asia Pacific to dominate the Market Due to Technological Advancements
The dominance in the flux-coated preforms market share is expected to be prominently influenced by the Asia-Pacific region. With robust industrialization, a burgeoning electronics sector, and a continuous focus on technological advancements, countries in Asia-Pacific, particularly China, Japan, and South Korea, are poised to play a pivotal role. These nations boast extensive manufacturing capabilities, driving the demand for flux-coated preforms in electronics assembly. Additionally, the region's strategic position as a global manufacturing hub positions it at the forefront of market growth. As industries in Asia-Pacific continue to expand, the region is likely to maintain its dominant role in shaping the trajectory of the flux-coated preforms market.
KEY INDUSTRY PLAYERS
Key Industry Players Shaping the Market through Innovation and Market Expansion
Major industry players are significantly influencing the flux-coated preforms market through a combination of innovation and strategic market expansion. These key players are at the forefront of driving change and shaping the industry landscape.
In terms of innovation, these influencers are actively developing and implementing advanced technologies and materials in flux-coated preforms, setting new standards for precision and performance in soldering processes. Simultaneously, strategic market expansion initiatives are being undertaken to strengthen global presence and tap into emerging markets. These players are proactively identifying opportunities for growth and adapting to evolving industry trends. Collectively, these industry leaders are not only responding to market dynamics but are actively molding and defining the future trajectory of the flux-coated preforms market.
List of Top Flux Coated Preforms Companies
- Ametek (U.S.)
- Alpha (U.S.)
- Kester (U.S.)
- Indium Corporation (U.S.)
- Pfarr (Austria)
- Nihon Handa (Japan)
- SMIC (Semiconductor Manufacturing International Corporation) (China)
- Harris Products (U.S.)
- AIM Solder (Canada)
- Nihon Superior (Japan)
INDUSTRIAL DEVELOPMENT
October 2021: A noteworthy industrial development in the flux-coated preforms market is the increasing integration of automation in the manufacturing processes. Automation technologies, including robotic systems and advanced machinery, are being deployed to enhance efficiency, precision, and scalability in the production of flux-coated preforms. This development not only accelerates the manufacturing pace but also ensures consistent quality, meeting the stringent demands of modern electronics assembly. As the industry embraces automation, it opens avenues for higher production capacities and elevates the overall competitiveness of the flux-coated preforms market.
REPORT COVERAGE
The flux-coated preforms market stands at the intersection of technological innovation, environmental considerations, and global industrial dynamics. While challenges such as environmental concerns pose hurdles, the industry is resilient, with key players driving innovation and market expansion. The shift towards miniaturization in electronic components and the rising adoption of renewable energy technologies act as powerful catalysts for market growth. As Asia-Pacific takes the lead in shaping the market, the infusion of automation emerges as a pivotal industrial development, streamlining production processes. The flux-coated preforms market is not just adapting; it is evolving, promising a future where precision soldering meets sustainability and technological advancement.
Attributes | Details |
---|---|
Market Size Value In |
US$ 0.1 Billion in 2023 |
Market Size Value By |
US$ 0.16 Billion by 2032 |
Growth Rate |
CAGR of 5.9% from 2024 to 2032 |
Forecast Period |
2024-2032 |
Base Year |
2024 |
Historical Data Available |
Yes |
Regional Scope |
Global |
Segments Covered |
|
By Type
|
|
By Application
|
FAQs
The flux coated preforms market is expected to reach USD 0.16 billion by 2032.
The flux coated preforms market is expected to exhibit a CAGR of 5.9% by 2032.
The driving factors behind the flux-coated preforms market include the relentless push for miniaturization in electronics and the increasing adoption of renewable energy technologies.
The flux coated preforms market segmentation that you should be aware of, which includes, based on types of flux coated preforms market is classified as leaded flux coated preforms, lead free flux coated preforms. Based on the application of the flux coated preforms market is classified as electronics, semiconductor, military & aerospace, medical, and others.