Micro-Mobility Market Size, Share, Growth, and Industry Analysis, By Type (Electric Bike, Electric Scooter, and Bicycle), By Application (Age 18-24, Age 25-34, and Age 35-44), and Regional Forecast to 2033
Trending Insights
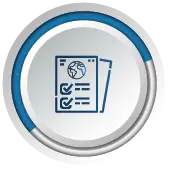
Global Leaders in Strategy and Innovation Rely on Our Expertise to Seize Growth Opportunities
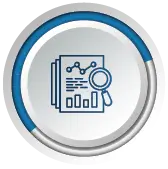
Our Research is the Cornerstone of 1000 Firms to Stay in the Lead
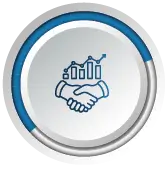
1000 Top Companies Partner with Us to Explore Fresh Revenue Channels
METAL BINDER JETTING 3D PRINTING MARKET OVERVIEW
The global metal binder jetting 3D printing market size expanded rapidly in 2022 and is projected to grow substantially by 2028, exhibiting a prodigious CAGR during the forecast period.
The metal binder jetting market is developing quickly as an innovative printing process that allows precise and waste-reduced production of complicated metal parts. The technology works by applying a binding solution selectively to a bed of metal powder, layer by layer and then using heat to connect the powder grains into a solid piece. The reasons more industries are embracing additive manufacturing are because it reduces production costs, speeds up the build process and makes it possible to make complex geometries that are challenging with older methods.
The growth of the market comes from the rising need for metal parts that are both light and sturdy and from new improvements in printing materials and technology. Important companies are devoting money to research and development to enhance the speed at which they print, the appearance of the parts and their toughness. Mass customization and demand for on-the-spot manufacturing is boosting the technology’s global growth. Still, post-processing needs and material constraints are present, but these are expected to be solved by the latest improvements which will make metal binder jetting a key booster for the 3D printing sector.
GLOBAL CRISES IMPACTING METAL BINDER JETTING 3D PRINTING MARKET
COVID-19 IMPACT
Metal binder jetting 3D printing Industry Had a Positive Effect Due to highlighted value of additive manufacturing during COVID-19 Pandemic
The pandemic started by disturbing the Metal Binder Jetting 3D Printing market through supply issues, closures of factories and slower research and design activities. Because many manufacturers struggled to get metal powders and binder agents, production moved at a slower pace. Companies in areas such as the aerospace and automotive industries are holding back both investments and expenses because of uncertainty and an economic downturn.
Still, the pandemic revealed that additive manufacturing, especially metal binder jetting, is ideal for quick prototyping and for making goods where and when they are needed. When medical equipment and components were in short supply, companies turned to 3D printing to make custom parts fast which promoted more interest in binder jetting. As a result, the recognition of these sectors should prompt the market to advance and expand since industries will shift toward flexible and resilient ways of manufacturing.
LATEST TREND
Integration of advanced automation and AI-driven process to Drive Market Growth
A recent trend in the Metal Binder Jetting 3D Printing sector is the use of automation and AI to achieve improved and consistent print results. Smart sensors and machine learning are being applied more by manufacturers to track printing and sintering in real time, support predictive maintenance, help correct defects and cut down on wasted materials. This development not only boosts production speed and lowers expenses, but also supports making binder jetting suitable for widespread use in aerospace and automotive, where being precise and repeatable is very important.
METAL BINDER JETTING 3D PRINTING MARKET SEGMENTATION
BY TYPE
Based on Type, the global market can be categorized into Fully Automatic and Semi-automatic
Fully Automatic: Once an automatic system is turned on, it proceeds all by itself using programmed equipment and machinery. High-efficiency, consistent and fast automation decrease the possibility of errors and reduce labor costs. Mostly, these are employed in mass production factories where there must be unbroken and uninterrupted output. Parts of automation include handling resources, printing samples, post-processing and checking the finished products for quality.
Semi-Automatic: Semi-automatic systems depend on humans to load goods, run the system and check the results. Though parts are automated to enhance efficiency and reduce how much operators have to manage, some tasks still need operator guidance and oversight. As both affordable and adaptable, it is appropriate for low volume runs or situations that need to be personalized. Semi-automatic systems help fill the gap between manual and automated ways of achieving things.
BY APPLICATION
Based on application, the global market can be categorized into Automotive, Aerospace & Defense, Medical and Others
Automotive: Using bendable metal binder jetting allows for the fabrication of metal parts that enhance a vehicle’s efficiency and performance. With this approach, organizations can rapidly design and produce limited batches of individualized parts, meaning they get their goods faster. With 3D printing, it is possible to manufacture metals for less cost than with traditional methods.
Aerospace & Defense: It is in aerospace and defense that metal binder jetting is applied to create strong parts with ideal weight, helping to save fuel and increase performance. It is useful for making complex-shaped components that cannot be produced quickly by standard machining techniques. With the use of technology, designers are able to adapt more freely while still meeting all quality and safety requirements.
Medical: Metal binder jetting enables the manufacturing of medical tools and implants that follow the patient’s needs and are made from biocompatible metals. Making the device fit the patient better and work as it should improves the patient’s results. Also, it makes it possible to make complex devices at affordable prices, something that can be hard for traditional manufacturing companies.
MARKET DYNAMICS
DRIVING FACTORS
Cost Efficiency and Material Savings to Boost the Market
A factor in the metal binder jetting 3D printing market growth is the Cost Efficiency and Material Savings. Unlike traditional methods, like machining and casting which produce a lot of waste, binder jetting uses only the required amount of powder for each part. Because each layer of lamination is simple and cheap, the process becomes a good option for prototyping as well as producing smaller quantities of products.
Complex Geometry and Design Freedom to Expand the Market
By using binder jetting, it becomes possible to make parts from metal that are too complex for traditional methods. This capability enables the development of lightweight structures, channels within parts and lattice networks, all valuable in aerospace, automotive and medical industries wanting to enhance performance and cut weight. The new technology is able to print multiple parts fast and all at once during one printing session. Because of automation and post-processing advancements, investors benefit from more efficient turnaround and the ability to easily scale their prototypes into mass production at low cost.
RESTRAINING FACTOR
Post-Processing Complexity and Costs to Potentially Impede Market Growth
Parts printed using metal binder jetting need additional curing, sintering and infiltration treatments to get their intended mechanical properties and appearance. Such processes add time and expense, making the technology less attractive for those who simply want to keep their workflows simple. The available powders for binder jetting are fewer than those available in laser powder bed fusion. Since printed parts may not be as stable in density, toughness and look as expected, it is usually more difficult to make them suitable for strict aerospace and medical applications.
OPPORTUNITY
Mass customization and on-demand manufacturing To Create Opportunity for the Product in the Market
Customized and immediate manufacturing of parts is where metal binder jetting needs to go next for many industries like aerospace, automotive and healthcare. With recent progress in material science and automation, making complex parts in large numbers will become simpler and more efficient. Using Industry 4.0 technologies can boost both efficiency and the quality of products. By doing this, binder jetting becomes a main factor in driving new, ecologically friendly manufacturing processes.
CHALLENGE
Achieving consistent mechanical properties and surface Could Be a Potential Challenge for Consumers
One of the biggest future issues for metal binder jetting is guaranteeing its properties and smoothness are in compliance with strict industry and regulation requirements. For additive manufacturing to be accepted in important sectors, it must solve complex post-processing and reduce randomness in part quality. Another problem is ensuring that the technology grows without spending too much money. Combat these problems will require ongoing efforts of both developing and standardizing new solutions.
METAL BINDER JETTING 3D PRINTING MARKET REGIONAL INSIGHTS
● NORTH AMERICA
North America is the fastest-growing region in this market. The United States metal binder jetting 3D printing market has been growing exponentially owing to multiple reasons. Demand from the aerospace, automotive and healthcare sectors is leading to fast growth in the Metal Binder Jetting 3D Printing market in North America. Innovation and the use of new technology grow rapidly due to major investments in research and the presence of important providers. The region is equipped with updated infrastructure and the government supports activities in additive manufacturing. One form of 3D printing called binder jetting is being tried by startups and established manufacturers for both developing prototypes and manufacturing items in larger volumes.
● EUROPE
Europe’s metal binder jetting market is steadily increasing because of its interest in automation and eco-friendly manufacturing. There is significant progress because Germany, France and the UK have made sizeable investments and teamed up researchers and industry experts. Binder jetting is widely used by aerospace and automotive companies for building parts that are both lightweight and complex. Moreover, strict environmental laws help make binder jetting a more appealing option in production.
● ASIA
Metal binder jetting is becoming important in Asia as industrialization increases and people in China, Japan and South Korea are using it more. The area has a big manufacturing sector and more investments in 3D printing are happening. Efforts to make industrial binders and parts more affordable have encouraged use of binder jetting technology in the auto, electronics and medical sectors. Smart manufacturing is helping the market grow because of what governments are doing to support it.
KEY INDUSTRY PLAYERS
Key Industry Players Shaping the Market Through Innovation and Market Expansion
Key industry players are shaping the metal binder jetting 3D printing marketplace through strategic innovation and market expansion. These companies are introducing advanced techniques and processes to improve the quality and performance of their offerings. They are also expanding their product lines to include specialized variations, catering to diverse customer preferences. Additionally, they are leveraging digital platforms to increase market reach and enhance distribution efficiency. By investing in research and development, optimizing supply chain operations, and exploring new regional markets, these players are driving growth and setting trends within the metal binder jetting 3D printing market.
LIST OF TOP METAL BINDER JETTING 3D PRINTING COMPANIES
• ExOne [U.S.]
• Digital Metal [Sweden]
• GE Additive [U.S.]
• Stratasys [U.S.]
• 3D Systems [U.S.]
KEY INDUSTRY DEVELOPMENT
November 2022: In November 2022, Desktop Metal unveiled the Shop System Pro, the most advanced version of its Shop System metal binder jetting technology. Made for high-volume users, it allows for greater adjustment and control of costs and machine functions. Within the system, custom printing, printing in both directions and custom sintering profiles are available, so users can design their processes to best fit different uses or price points. The update is for manufacturers wanting to work with their own or third-party powder materials, increasing the flexibility of binder jetting for industrial jobs.
REPORT COVERAGE
The study offers a detailed SWOT analysis and provides valuable insights into future developments within the market. It explores various factors driving market growth, examining a broad range of market segments and potential applications that may shape its trajectory in the coming years. The analysis considers both current trends and historical milestones to provide a comprehensive understanding of the market dynamics, highlighting potential growth areas.
The metal binder jetting 3D printing market is poised for significant growth, driven by evolving consumer preferences, rising demand across various applications, and ongoing innovation in product offerings. Although challenges such as limited raw material availability and higher costs may arise, the market's expansion is supported by increasing interest in specialized solutions and quality improvements. Key industry players are advancing through technological advancements and strategic expansions, enhancing both supply and market reach. As market dynamics shift and demand for diverse options increases, the metal binder jetting 3D printing market is expected to thrive, with continuous innovation and broader adoption fueling its future trajectory.
Attributes | Details |
---|---|
Market Size Value In |
US$ 0.8 Billion in 2024 |
Market Size Value By |
US$ 1.5 Billion by 2033 |
Growth Rate |
CAGR of 7.1% from 2024 to 2033 |
Forecast Period |
2025 To 2033 |
Base Year |
2024 |
Historical Data Available |
Yes |
Regional Scope |
Global |
Segments Covered |
By Type
|
By Application
|
FAQs
The global Metal Binder Jetting 3D Printing Market is expected to reach USD 1.5 billion by 2033.
The Metal Binder Jetting 3D Printing Market is expected to exhibit a CAGR of 7.1% by 2033.
North America is the prime area for the Metal binder jetting 3D printing market owing to its strong adoption in aerospace, automotive, and medical sectors.
Complex Geometry and Design Freedom and Cost Efficiency and Material Savings are some of the driving factors in the market.
The key market segmentation, which includes, based on type, the Metal binder jetting 3D printing market is Fully Automatic and Semi-automatic. Based on application, the Metal binder jetting 3D printing market is classified as Automotive, Aerospace & Defense, Medical and Others.