What is included in this Sample?
- * Market Segmentation
- * Key Findings
- * Research Scope
- * Table of Content
- * Report Structure
- * Report Methodology
Download FREE Sample Report
Metallurgical Grade Silicon Metal Market Size, Share, Growth, and Industry Analysis, By Type (Silicon Metal, Silicon Alloys and Metallurgical-Grade Silicon), By Application (Solar Panels, Electronics, Semiconductors and Steel Industry), and Regional Forecast to 2034
Trending Insights
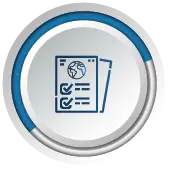
Global Leaders in Strategy and Innovation Rely on Our Expertise to Seize Growth Opportunities
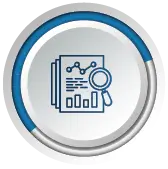
Our Research is the Cornerstone of 1000 Firms to Stay in the Lead
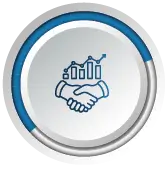
1000 Top Companies Partner with Us to Explore Fresh Revenue Channels
METALLURGICAL GRADE SILICON METAL MARKET OVERVIEW
The global Metallurgical Grade Silicon Metal Market was valued at USD 7.92 billion in 2025 and is expected to grow to USD 8.29 billion in 2026, reaching USD 11.91 billion by 2034, with a projected CAGR of about 4.63% during the forecast period 2026-2034.
Underlying aluminum alloys, silicones, and semiconductor manufacture, the metallurgical-grade silicon metal market has a vital role inside the worldwide materials environment. Fast-growing solar, electronics, and automotive value chains absolutely need it because of its heat resistance and conductivity. Growing demand for lightweight alloys in electric vehicles is increasing use even further. Quick urbanization in developing nations maintains a strong construction-related sector. Stricter sustainability regulations are also pushing manufacturers to use low-carbon smelting techniques. Consistent R&D is elevating purity levels, therefore opening sophisticated electronic applications. With Asia serving as both the biggest supplier and consumer, global trade patterns are still active. Together, these powers put metallurgical silicon as a key raw material for a decarbonizing economy.
METALLURGICAL GRADE SILICON METAL MARKET KEY FINDINGS
- Market Size and Growth: With a compound annual growth rate (CAGR) of 4.63% from 2024 to 2033, the global market for metallurgical-grade silicon metal is projected to reach USD 11.38 billion by 2033, up from USD 7.57 billion in 2024 to USD 7.92 billion in 2025.
- Key Market Driver: Approximately 95% of all solar modules sold in 2022 were silicon-based, and the material's crucial role in renewable energy was highlighted by the rise in solar PV generation, which went from 270 TWh to nearly 1,300 TWh.
- Major Market Restraint: The high production costs of 1 ton of silicon metal are caused by the need for about 2.8 tons of quartz and 13,000 kWh of energy.
- Emerging Trends: According to the U.S. Geological Survey (USGS), China produced about 70% of the world's silicon metal in 2023, with an estimated 8 million metric tons produced worldwide.
- Regional Leadership: In 2024, China produced about 80% of the world's silicon, demonstrating its substantial market power.
- Competitive Landscape: With 3,900,000 metric tons of silicon metal produced in 2024, China accounted for about 80% of the world's silicon production.
- Market Segmentation: The production of steel makes up 33.7% of the market, while aluminum casting comes in second at 29.4%.
- Recent Development: Elkem ASA declared plans to invest $150 million to increase its capacity to produce silicon metal in Norway.
COVID-19 IMPACT
COVID-19 disrupted supply chains, hindering metallurgical silicon market growth
The global COVID-19 pandemic has been unprecedented and staggering, with the market experiencing lower-than-anticipated demand across all regions compared to pre-pandemic levels. The sudden market growth reflected by the rise in CAGR is attributable to the market’s growth and demand returning to pre-pandemic levels.
As lockdowns stopped automobile, construction, and consumer-electronics manufacture, the epidemic delivered an instant hit to metallurgical silicon demand. Severe container shortages and port congestion slowed down quartz and charcoal deliveries, therefore reducing furnace usage. South America and South Africa's temporary mine shutdowns increased the scarcity of unprocessed resources. Deferred capital expenditures on fresh smelters brought the planned increases in capacity to a halt. As supplies grew, spot costs dropped, reducing producer margins and causing plant closures. Restrictions on personnel and health regulations increased running costs, therefore destroying profitability. Sales volumes in 2022 were still below 2019 levels even if the late-2021 stimulus revived some downstream industries. COVID-19 showed the market's vulnerability to brittle logistics and synchronized worldwide shocks.
LATEST TRENDS
Market Growth Driven by Cleaner, Smarter Silicon Production and Recycling
As countries seek net-zero targets, demand for solar-grade silicon increases, forcing metallurgical manufacturers to provide purer feedstock for polysilicon transformation. AI-driven process control is becoming increasingly important in smelters, optimizing energy use and cutting carbon footprints. Hydrogen-based reduction trials promise to cut CO₂ emissions against conventional carbon-intensive routes. Automakers are specifying higher-silicon aluminum alloys to meet light weighting objectives for EV battery casings. Recycling of silicon-rich dross from foundries is emerging as a circular-economy opportunity. Governments are encouraging furnace upgrades by providing tax incentives for green energy that counteract expensive power costs. Digital twins let predictive maintenance be done, therefore lowering unplanned downtime. Together, these developments are guiding the sector toward more resilient, cleaner, and smarter operations.
METALLURGICAL GRADE SILICON METAL MARKET SEGMENTATION
By Type
Based on Type, the global market can be categorized into Silicon Metal, Silicon Alloys and Metallurgical-Grade Silicon
- Silicon Metal: With a purity of around 98–99%, silicon metal serves as a hardener in aluminum alloys, boosting strength, fluidity, and thermal stability. Silicone polymers found in adhesives, sealants, and medical equipment benefit from their chemical inertness. Demand is increasing as solar wafer manufacturers guarantee upstream supply to counter polysilicon shortages. Silicon metal acts as a reductant for high-value, specialized chemicals in chemical processing. Large-scale developments in Yunnan province of China are moving output toward renewable hydropower, hence lowering emission intensity. To satisfy local chip programs, North America is improving smelting capacity. Price swings still depend on coal availability and energy prices. Governmental strategic stockpiling is now fairly frequent to soften supply shocks.
- Silicon Alloys: During steelmaking, silicon alloys—mostly ferrosilicon, silicomanganese, and magnesium-silicon—provide deoxidizing and grain-refining advantages. Demand for ferrosilicon follows worldwide crude-steel production, with India and the ASEAN bloc offering fresh growth prospects. High-purity inoculant alloys improve cast-iron machinability, essential for automotive engine components. Producers are experimenting with low-carbon ferroalloys using biomass-based reductants to satisfy ESG requirements. Alloy blend customization is rising, tailored to advanced electrical steels for EV motors. The demand for high-strength steels in the aerospace industry also favors premium alloy grades. Export tariffs by top suppliers like Russia can quickly impact spot markets. Future consumption will depend on infrastructure simulation and advancements in steelmaking technologies.
- Metallurgical-Grade Silicon: At 1,600 °C in submerged-arc furnaces, metallurgical-grade silicon (~98% purity) is smelted from quartz and carbonaceous reductants. It serves as the main precursor for upgraded metallurgical-grade (UMG) silicon used in cost-sensitive solar cells. Manufacturers are adjusting furnace charge ratios to increase yield and reduce electrode wear. Slag recycling innovations recover valuable silica, hence lowering input costs and trash. Pilot facilities are marketing "low-carbon silicon" at a premium using green electricity. End users increasingly audit suppliers for traceability, hence favoring vertically integrated operations. Price benchmarks follow negotiated quarterly contracts in China, Norway, and Brazil. Despite energy hurdles, capacity expansions continue to align with polysilicon demand. Met-grade silicon hence remains the pillar of the supply chain for downstream high-purity goods.
By Application
Based on application, the global market can be categorized into Solar Panels, Electronics, Semiconductors and Steel Industry
- Solar Panels: Photovoltaic companies use metallurgical silicon that gets upgraded into polysilicon and ingots to slice wafers. India, the US, and the EU are seeing record solar auction volumes, which is pushing up demand. Advanced PERC and TOPCon cells need feedstock with stricter impurity limits to work. Gigafactories in Southeast Asia and the Middle East are signing long-term deals with smelters to guarantee steady supplies. Governments are using green bonds to fund dedicated solar-grade silicon plants to maintain supply control. Researchers are exploring direct metallurgical methods to avoid costly and energy-heavy chemical vapor deposition. Recycling old panels could generate a new flow of silicon after 2030. Overall, solar energy is still the fastest-growing application.
- Electronics: Silicon metal plays a critical part in creating chips, sensors, and power components found in both consumer gadgets and industrial tools. Growing IoT and edge computing trends have fueled a rising need to produce wafers in 200 mm and 300 mm manufacturing plants. Silicone-based encapsulants made using silicon metal protect delicate circuits from heat and moisture damage. Electronics manufacturing hubs across Asia depend on silicon imports to feed chemical processing units. Many governments are trying to set up local chip-making facilities to avoid risks linked to international politics. High-tech flexible devices now require pure silicon as their foundation. Re-shoring policies in the U.S. could lead to a higher demand for smelters within nearby areas. As technology evolves, this industry looks to keep expanding further.
- Semiconductors: Almost all devices and technologies depend on semiconductors to function. These materials make modern electronics like smartphones and computers work. They allow electricity to flow, but not as well as metals. This makes them ideal to control electric currents. Technology advances would not happen without them. Researchers aim to make semiconductors more effective. Manufacturers take metallurgical-grade silicon and purify it into polysilicon with over 99.9999 percent purity. This forms the base material needed for memory and logic chips. Making chips smaller than 5 nm demands metal-free materials, pushing up purification costs. To get high-quality silicon, foundries in the US, Taiwan, and South Korea agree to long-term supply deals. The demand for processors used in AI systems, 6G research, and data centers keeps wafer production levels stable to meet needs. Silicone-based products also assist in advanced semiconductor packaging for die-attach and heat management. Even so, the chip industry’s cyclical nature leads to unstable silicon spot-market transactions.
- Steel Industry: The steel industry holds a major place in construction and modern building projects. It supplies essential materials to build infrastructure and make products. Its manufacturing processes have a significant effect on economies around the globe by shaping development and growth. This sector provides countless jobs, making it a vital part of many communities. New ways of production aim to cut costs and produce stronger steel. Recycling steel is growing to achieve environmental objectives. Expanding infrastructure investments in developing nations is fueling the use of silicon-rich long steel products. The popularity of electric arc furnaces boosts the demand for silicon-based additives required to meet specific steelmaking standards. Steel ladles now use longer-lasting linings made with more silicon ceramics.
MARKET DYNAMICS
Market dynamics include driving and restraining factors, opportunities and challenges stating the market conditions.
Driving Factors
Solar Power Installations Are Growing Driving Growth
Massive spending on large-scale solar arrays is driving the demand for high-purity silicon more than anything else. Feed-in tariffs and standards that push for renewable energy are speeding up the worldwide installation of solar panels. Big tech companies sign long-term power deals, which guarantee massive demand for solar energy. Countries with lots of sunlight are adding solar systems with storage at record rates, spreading the demand across more regions. Advanced solar cells like heterojunction (HJT) need pure silicon, leading to higher requirements for purity. With the cost of solar power falling , its economics remain attractive. To keep up, manufacturers are rushing to get their silicon certified for solar use. This growing cycle cements solar power as a key factor driving demand.
Growth in the Automotive and Construction Fields Fueling Demand
As electrification changes the automotive industry, automakers are using lightweight aluminum-silicon alloys to construct battery packs, motor housings, and chassis. Manufacturers are being forced to use alloys with a higher silicon content due to stricter CO₂ and safety regulations. Strong, corrosion-resistant steel is needed in the booming post-pandemic cities in Asia and Africa, which increases demand for ferrosilicon. Architects are also using 3-D printing to make heat-resistant building components using silicon-rich powders. The indirect demand for alloys in infrastructure projects has increased as a result of significant government funding for railroads, bridges, and smart-grid systems. In order to make buildings weatherproof, prefabricated construction techniques rely on silicone-based sealants. Together, the expansion of the infrastructure and transportation industries promotes the steady use of silicon, converting more general economic activity into actual silicon consumption.
Restraining Factor
High Energy Costs and Policies Hinder Silicon Metal Market Growth
Turning quartz into silicon metal uses as much as 13 MWh per ton, making costs depend on electricity prices and carbon taxes. Climate policies make places with fossil-fuel grids face tougher scrutiny, making companies hesitate to set up new furnaces. The EU’s carbon-border-adjustment rules aim to tax imports that have high emissions, putting profit margins under pressure. Unstable prices for coal and coke make it harder for smelters to plan costs. Local communities often resist large smelting plants, which can slow down permits and increase compliance costs. Uneven availability of affordable renewable energy makes some areas better for production than others. High energy use remains the biggest roadblock to unlimited capacity expansion. Though there are energy-saving technologies, they involve high upfront expenses and have not been adopted yet.
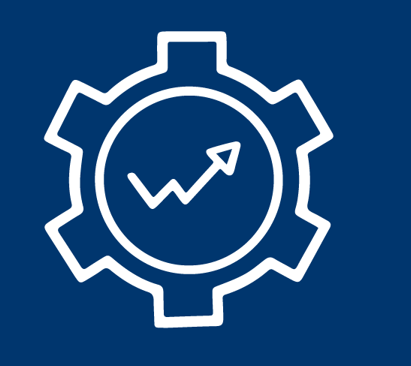
Innovations Drive Market Growth by Enhancing Silicon Purity and Efficiency
Opportunity
Advanced carbothermic reactors with systems that recycle off-gases reduce energy usage and generate earnings from by-products like carbon monoxide for the Metallurgical Grade Silicon Metal Market Growth. Plasma-torch refining reaches higher heat levels to remove more impurities. Digital sensors and machine learning adjust electrode placements, which reduces unexpected stoppages. Hydrometallurgical treatments take out boron and phosphorus, helping produce solar-grade silicon without using expensive Siemens tech.
Small modular smelters using renewable power allow quartz-rich but remote areas to begin production. Producers use life-cycle tools to market low-carbon silicon at higher prices. Government-funded R&D programs push these technologies toward wider adoption. These innovations aim to boost purity levels while preventing a rise in energy consumption.
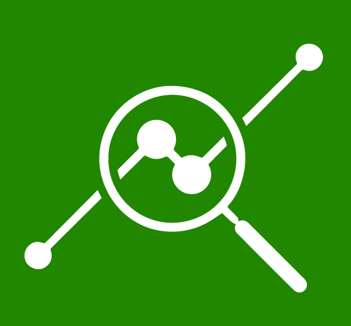
Market Growth Faces Hurdles from Supply, Logistics, and Sourcing Challenges
Challenge
Mining quartz runs into challenges like land disputes and stricter environmental permits, which reduce ore availability. Charcoal and certain types of low-ash coal are harder to get due to limits on deforestation and the shutdown of some mines. Tensions between countries put shipping routes for key materials like wood chips and coke at risk. During the pandemic, clogged-up ports exposed weaknesses in relying on just one supply route to get seaborne materials.
Relying on just-in-time inventory systems also showed its flaws, so companies now keep extra stock, though it ties up money. Buyers down the chain now use security-of-supply checks to decide how contracts get assigned. Setting up multiple diverse supply networks in different regions takes a lot of money and effort. Long-term, making logistics more secure and reliable is still a big uphill battle.
-
Request a Free sample to learn more about this report
METALLURGICAL GRADE SILICON METAL MARKET REGIONAL INSIGHTS
-
North America
North America's Metallurgical Silicon Market Growth Driven by Innovation, Policy
North America takes the lead due to its rich quartz resources, cutting-edge smelting techniques, and strong industries that use silicon in their products. Clean-energy incentives from the government speed up the growth of domestic polysilicon production and increase the demand for metallurgical feedstock. Goals to electrify cars boost the need for lighter aluminum-silicon alloys. The United States Metallurgical Grade Silicon Metal Market benefits from cheaper electricity powered by shale gas in the Pacific Northwest. Policies like "Buy American" encourage electronics companies to get silicon from within the country, strengthening the local supply chain. Research and development hubs in Appalachia work on pilot projects to test cleaner smelting processes. Altogether, these elements solidify North America's role as a key player in this sector.
-
Europe
Europe's Green Policies and Tech Drive Metallurgical Silicon Market Growth
Europe aims to achieve climate neutrality and drives investment toward green Metallurgical Grade Silicon Metal Market Share. Producers in Norway use hydroelectric power to create and sell silicon metal with zero carbon emissions. The region’s strong car industry relies on aluminum-silicon wheels and engine blocks that perform well under demanding conditions. EU policies on carbon-border adjustments shield local smelters from competition with high-emission imports, helping them stay profitable. Efforts like the European Solar Alliance work to bring back PV supply chains, which increases the need for metallurgical silicon. Strict REACH laws push companies to reduce impurities. Europe, as a result, mixes sustainable practices with advanced technology.
-
Asia
Asia's Market Growth Thrives On Manufacturing, Energy Access, And Policy
Asia leads the world in production, with China alone accounting for over 60% of output and domestic use. Governments are adjusting quotas to shift manufacturing toward Yunnan and Sichuan, where hydropower reduces emissions. Countries like Japan and South Korea rely on importing top-grade silicon to produce electronics and EV batteries. India’s new Production-Linked Incentive policy is helping set up polysilicon factories, increasing the demand for raw materials within the country. Infrastructure growth tied to the Belt and Road Initiative drives up the need for steel and alloys across the region. Cheap energy and closeness to manufacturing hubs keep Asia's dominance in place. However, strict environmental regulations might soon shut down older coal-heavy furnaces. Asia continues to be the central hub of both manufacturing and consumption trends.
KEY INDUSTRY PLAYERS
Key Players Drive Innovation and Sustainability, Fueling Overall Market Growth
Big players like Ferroglobe PLC, Elkem ASA, RIMA Group, Mississippi Silicon LLC, and Hoshine Silicon Industry Co. steer the market's direction through their size, advanced technology, and strong partnerships. They invest a lot in automating furnaces, getting low-carbon energy, and merging processes downstream. This helps them manage both costs and quality more. Their collaborations with major solar and semiconductor companies ensure stable long-term deals, which add to steady income. Mergers and acquisitions combine resources and reduce competition while increasing leverage against suppliers of raw materials. Efforts like using biochar and testing carbon-capture systems support sustainability goals and allow companies to charge more for eco-friendly products. Inventing new products, like silicon with specific dopant levels, helps them stand out. Altogether, these strategies strengthen their market edge and grow the industry overall.
List of Top Metallurgical Grade Silicon Metal Companies
- Baidao Silicon Industry (China)
- Elkem ASA (Norway)
- HPQ Silicon Resources (Canada)
- Ferroglobe (U.K.)
- Silicor Materials (U.S.)
KEY INDUSTRY DEVELOPMENT
June 2021: Ferroglobe PLC launched a big project to upgrade furnaces and fix bottlenecks at its Sabón plant in Spain, aiming to boost silicon metal production by 55 kt. The move responded to growing demand from Europe’s polysilicon producers shifting to high-efficiency TOPCon cells. The upgrades included better electrode controls and a system to recover waste heat, which lowered energy use by 8 %. Ferroglobe secured long-term supply deals with solar-glass makers to ensure steady business. The project created 120 skilled jobs, helping the local economy bounce back after COVID. By boosting Europe’s ability to produce low-carbon silicon, the expansion supports the EU’s Green Deal goals. This achievement shows how leading companies plan investments to meet clean-energy trends and gain profits.
REPORT COVERAGE
The study encompasses a comprehensive SWOT analysis and provides insights into future developments within the market. It examines various factors that contribute to the growth of the market, exploring a wide range of market categories and potential applications that may impact its trajectory in the coming years. The analysis takes into account both current trends and historical turning points, providing a holistic understanding of the market's components and identifying potential areas for growth.
This research report examines the segmentation of the market by using both quantitative and qualitative methods to provide a thorough analysis that also evaluates the influence of strategic and financial perspectives on the market. Additionally, the report's regional assessments consider the dominant supply and demand forces that impact market growth. The competitive landscape is detailed meticulously, including shares of significant market competitors. The report incorporates unconventional research techniques, methodologies and key strategies tailored for the anticipated frame of time. Overall, it offers valuable and comprehensive insights into the market dynamics professionally and understandably.
Attributes | Details |
---|---|
Market Size Value In |
US$ 7.92 Billion in 2025 |
Market Size Value By |
US$ 11.91 Billion by 2034 |
Growth Rate |
CAGR of 4.63% from 2025 to 2034 |
Forecast Period |
2025 - 2034 |
Base Year |
2024 |
Historical Data Available |
Yes |
Regional Scope |
Global |
Segments Covered |
|
By Type
|
|
By Application
|
FAQs
The global Metallurgical Grade Silicon Metal Market is expected to reach USD 11.91 billion by 2034.
The Metallurgical Grade Silicon Metal Market is expected to exhibit a CAGR of 4.63% by 2034.
Solar Power Installations Are Growing & Growth in the Automotive and Construction Fields to expand the market growth.
The key market segmentation, which includes, based on type, the Metallurgical Grade Silicon Metal Market is Silicon Metal, Silicon Alloys and Metallurgical-Grade Silicon. Based on application, the Metallurgical Grade Silicon Metal Market is classified as Solar Panels, Electronics, Semiconductors and Steel Industry.