What is included in this Sample?
- * Market Segmentation
- * Key Findings
- * Research Scope
- * Table of Content
- * Report Structure
- * Report Methodology
Download FREE Sample Report
Offsite Construction Market Size, Share, Growth, and Industry Analysis, By Type (Prefab Construction for Permanent Building, Modular Construction for Relocatable Building), By Application (Residential, Commercial, Industrial), and Regional Forecast to 2033
Trending Insights
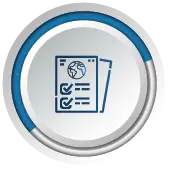
Global Leaders in Strategy and Innovation Rely on Our Expertise to Seize Growth Opportunities
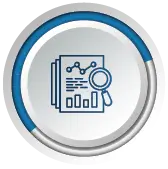
Our Research is the Cornerstone of 1000 Firms to Stay in the Lead
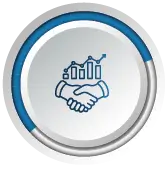
1000 Top Companies Partner with Us to Explore Fresh Revenue Channels
OFFSITE CONSTRUCTION MARKET OVERVIEW
The offsite construction market size was valued at USD 120.98 billion in 2024 and is expected to reach USD 186.31 billion by 2033, growing at a compound annual growth rate (CAGR) of 4.9% from 2025 to 2033.
The Offsite Construction Market is unexpectedly evolving as the development organization seeks to beautify overall performance, reduce undertaking timelines, and reduce the environmental effects. Offsite manufacturing involves the prefabrication, modularization, and penalization of building components in managed manufacturing facility settings that are transported to the website for speedy meetings. This technique gives numerous blessings over traditional creation techniques, with progressed best management, decreased waste, and significant time and financial savings. Technological improvements, such as building information modeling (BIM), automation in production, and digital assignment management systems, are further being used in offsite creation. Additionally, developing exertion shortages, developing urbanization, and a growing emphasis on sustainable constructing practices have located offsite production as a key technique for modernizing the development enterprise.
However, the marketplace faces numerous demanding situations that would avert its good-sized adoption. High upfront funding fees for setting up dedicated offsite production facilities, transportation logistics, and integration with cutting-edge on-website strategies can be significant limitations. Traditional creation practices, regulatory hurdles, and resistance to alternate from set-up enterprise gamers also progressively transitioned to offsite methods. Despite those challenges, the offsite introduction marketplace presents ample opportunities for boom, especially in rising markets wherein fast urbanization and infrastructure development are commonplace. Innovations in prefab generation and the combination of sustainable practices provide the potential for rate reductions and extra appropriate layout flexibility, paving the way for a more green, safer, and environmentally pleasant destiny in creation.
COVID-19 IMPACT
Offsite Construction Industry Had a Negative Effect Due to Reduced Capital Investment during the COVID-19 Pandemic
Economic uncertainty during the pandemic led to tighter budgets and the postponement of investments in offsite production facilities and advanced technology. Global lockdowns and shipping restrictions led to delays and shortages of crucial prefabricated components and raw substances. Health restrictions and personnel barriers in manufacturing unit settings decreased manufacturing potential and slowed down element manufacturing. Border closures and tour restrictions complicated the motion of prefabricated modules from factories to construction websites, inflicting delays.
The pandemic spurred a speedy shift in the direction of offsite construction as agencies sought more secure, socially distant strategies to retain constructing tasks. With strict social distancing and lockdown measures, offsite creation minimized the want for massive onsite crews, making sure of venture continuity. Controlled manufacturing unit environments allowed for greater steady fine and adherence to health protocols, reducing the threat of contamination and transformation.
LATEST TREND
Growing Focus on Sustainability to Drive Market Growth
Growing Focus on Sustainability are vital benefits of offsite construction market share. The developing focus on sustainability is a prime driving force behind adopting offsite creation techniques. Compared to conventional on-internet site manufacturing, offsite production offers massive environmental benefits. Manufacturing in controlled factory environments allows optimized material manipulation. Precise measurements and cutting techniques, coupled with minimized material control, notably reduce waste generation at a few stages in the fabrication technique. Improved control inside the manufacturing unit minimizes the need to transform because of defects, further reducing fabric loss. This efficient use of assets promotes sound aid performance and reduces the overall environmental footprint of advent tasks. Furthermore, the controlled factory surroundings make it less difficult to incorporate sustainable substances and layout principles. For instance, factories can, without trouble, utilize recycled content material materials, domestically sourced wood, and distinctive green building components. The modular nature of offsite Advent additionally allows for designs that optimize electricity performance, consisting of prefabricated wall panels with immoderate insulation values. The capability to prefabricate building elements off-site reduces on-website manufacturing waste, noise pollutants, and disruption to the encircling environment. In essence, offsite manufacturing gives a pathway to greener construction practices by minimizing waste, promoting overall performance, and facilitating the mixing of sustainable materials and layout.
OFFSITE CONSTRUCTION MARKET SEGMENTATION
By Type
Based on Type, the global market can be categorized into Prefab Construction for Permanent Building, Modular Construction for Relocatable Building.
- Prefab Construction for Permanent Building: Involves assembling pre-manufactured components on-website to create durable, lengthy-term structures with enhanced quality control and efficient construction timelines.
- Modular Construction for Relocatable Building: Utilizes standardized, prefabricated modules for smooth disassembly and relocation, imparting flexibility and value-effective answers for brief or adaptable structures.
By Application
Based on application, the global market can be categorized into Residential, Commercial, Industrial.
- Residential: Offsite creation in residential tasks allows the quicker, cost-powerful, and extraordinary meeting of houses and condominium units, improving affordability and layout consistency.
- Commercial: In business trends, offsite production streamlines the construction of workplaces, retail areas, and public centers, providing fast deployment and bendy layout to satisfy various enterprise needs.
- Industrial: Industrial packages leverage offsite production to fast gather factories, warehouses, and production centers with robust, scalable designs that guide high-call for operations.
MARKET DYNAMICS
Market dynamics include driving and restraining factors, opportunities and challenges stating the market conditions.
Driving Factors
Accelerated Urbanization to Boost the Market
A factor in the offsite construction market growth is accelerated urbanization. Rapid urban boom and the rising want for housing, schools, hospitals, and different public infrastructure in both developed and rising markets are adopting offsite creation methods that provide quicker construct times and scalable answers. Offsite production drastically reduces on-site exertions and creation time by prefabricating components in controlled environments. This performance results in fee financial savings in hard work, substances, and venture control, making it an attractive alternative for developers and contractors. Manufacturing constructing components in factory settings allows for more incredible first-rate guarantee and consistency, resulting in advanced product performance and reduced rework or delays compared to standard production methods.
Technological Advancements in Production to Expand the Market
Technological advancements in production are another critical aspect of the offsite construction market. Innovations in virtual design equipment (which include Building Information Modeling), robotics and automation have stepped forward the precision and efficiency of offsite creation. These technologies permit detailed planning, correct meetings, and mixing clever systems for ongoing performance monitoring. Offsite production generates less waste, uses fewer assets, and offers better energy performance. With the growing international consciousness of sustainable building practices, those environmental advantages are increasingly valued with the aid of regulators and clients. Many governments are selling offsite creation through incentives, subsidies, and favorable policies that reduce creation time, lower emissions, and enhance construction first-rate, thereby accelerating market adoption. The marketplace is pushed to employ a growing preference for modular production, which offers flexibility in layout and can be easily improved or reconfigured. This fashion particularly appeals to regions dealing with housing shortages or needing fast infrastructure improvement.
Restraining Factor
Transportation Challenges and High Cost to Potentially Impede Market Growth
Prefabricated modules must be transported from factories to creation websites, which may be complicated and high-priced, particularly in urban areas with congested visitors or far-off locations with limited infrastructure. Establishing offsite production centers and acquiring advanced technology requires significant premature investments, which can be a barrier for smaller corporations and sluggish marketplace penetration. Seamlessly integrating prefabricated additives into existing on-web page construction practices may be challenging. Variations in design tolerances and placement situations may additionally result in compatibility issues and require additional modifications. Offsite creation regularly is based on standardized modules and techniques that can restrict architectural creativity and limit customization options for tasks with precise design necessities. Transitioning from traditional to offsite construction methods calls for specialized schooling and understanding. A scarcity of professionals familiar with advanced production and virtual construction technologies can preclude implementation.
Opportunity
Public-Private Partnerships To Create Opportunity for the Product in the Market
Collaborations between government and personal production corporations can facilitate massive-scale infrastructure projects that depend upon offsite construction methods, ensuring regular marketplace demand and monetary assistance. Addressing housing shortages through the scalable, quick deployment of modular and prefabricated homes gives a moneymaking possibility, especially in densely populated city facilities and unexpectedly growing regions. Further integration of IoT, AI, and BIM in offsite creation can decorate assignment planning, excellent manipulation, and operational efficiency. These technological advancements offer a competitive edge and can lead to new service offerings. The worldwide push for sustainable creation opens possibilities for offsite manufacturers to innovate eco-friendly building materials and approaches, appealing to environmentally conscious purchasers and regulatory our bodies. Opportunities exist to tailor offsite construction solutions for specialized sectors, which include healthcare, training, and disaster remedy, where rapid deployment and outstanding results are essential.
Challenge
Maintaining Quality Could Be a Potential Challenge for Consumers
Ensuring that offsite manufactured components meet brilliant requirements and are steady throughout more than one batch may be challenging, specifically when scaling production for significant initiatives. The inherent standardization in offsite creation can restrict design flexibility, making it difficult to fulfill the bespoke desires of clients who require distinctly customized architectural answers. The giant initial investments necessary for generation, device, and facility setup pose financial dangers, especially for small and medium enterprises. These expenses can be a considerable barrier in economically risky regions. Coordinating the complex delivery chain—from sourcing raw materials to transporting huge prefabricated modules—demands sophisticated logistics management. Disruptions in any part of the supply chain can postpone initiatives and increase costs. Offsite construction techniques regularly face regulatory challenges because of differences in construction codes and zoning policies across areas. Navigating this fragmented regulatory environment adds complexity and might cause sluggish undertaking approvals.
Request a Free sample to learn more about this report
OFFSITE CONSTRUCTION MARKET REGIONAL INSIGHTS
-
North America
North America is the fastest-growing region in this market. The United States offsite construction market has been growing exponentially for multiple reasons. North America is the main place for offsite production, and it is characterized by advanced technological integration and a strong consciousness of efficiency and sustainability. In the U.S. and Canada, the market benefits from robust construction interest, mature regulatory surroundings, and extensive adoption of virtual layout tools, including BIM and automated manufacturing processes. Major stakeholders inside the area have embraced offsite methods to lessen creation timelines and labor fees, address growing environmental worries, and strict noise and waste policies. Additionally, the vicinity's emphasis on innovation has caused extended investments in modular and prefabricated answers for each residential and industrial task. Despite challenges, which include high initial capital charges and logistical hurdles in transporting prefabricated modules, North America keeps powering the adoption of offsite production through ongoing technological improvements and supportive authorities incentives.
-
Europe
Europe's offsite creation market is nicely-established, driven by strong regulatory frameworks, a focal point on sustainability, and a culture of first-class craftsmanship. Key markets within the U.K., Germany, France, and the Nordics are pushing the envelope with eco-friendly constructing practices, integrating offsite construction to meet stringent strength performance and environmental requirements. European companies leverage advanced production techniques to produce tremendous prefabricated additives that beautify assignment speed and decrease production waste. Furthermore, the emphasis on green building projects and smart infrastructure has spurred public and private investments in modular production answers, mainly for large-scale industrial, public, and residential traits. However, challenges that include high production costs and varying regulatory requirements across distinctive international locations require organizations to constantly innovate and adapt their enterprise fashions.
-
Asia
The Asia-Pacific region is rising as one of the fastest-developing markets for offsite creation, fueled by using fast urbanization, infrastructure improvement, and a growing center-elegance population. Countries like China, India, Japan, and South Korea are witnessing giant investments in modular creation, pushed by the desire for quicker, value-effective, and sustainable building answers in densely populated urban areas. Local governments in emerging economies are increasingly selling offsite creation to alleviate housing shortages and improve the efficiency of infrastructure projects. Additionally, technological advancements and virtual equipment integration in production procedures support decorating products first-rate and decreasing production time. Despite demanding situations such as fragmented regulatory environments, deliver chain constraints, and the need for professional exertions, Asia-Pacific remains a key growth engine, imparting enormous opportunities for growth and innovation in offsite construction.
KEY INDUSTRY PLAYERS
Key Industry Players Shaping the Market Through Innovation and Market Expansion
Key employer gamers inside the offsite production marketplace use enterprise transformation through strategic innovation and growth. These agencies are adopting advanced production and layout strategies and modern construction techniques to decorate prefabricated construction components' pleasant, efficient, and aesthetic enchantment. They are broadening their provider portfolios to include specialized alternatives consisting of modular, hybrid, and customizable constructing systems, catering to the numerous desires of clients—in particular, in rapidly urbanizing and emerging markets. Additionally, those organizations are leveraging digital technology to boost market visibility, streamline task management and sales strategies, and optimize delivery chain networks, ensuring more get admitted to offsite creation solutions, particularly in regions challenged by conventional constructing boundaries. By investing in studies and development, improving logistical operations, and tapping into untapped local markets, these players are riding a boom and fostering non-stop advancements inside the offsite creation industry.
List of Top Offsite Construction Companies
- Daiwa House (Japan)
- Clayton Homes (U.S.)
- Laing O'Rourke (U.K.)
- BoKlok (Sweden)
- ATCO (Canada)
- FLUOR (U.S.)
- Red Sea International (Saudi Arabia)
KEY INDUSTRY DEVELOPMENT
December 2024: Element5, a leading mass wood creation corporation, introduced the growth of its mass wooden production facility to fulfill the growing demand for sustainable construction substances inside the offsite production market. This enlargement will grow production capability for pass-laminated wooden (CLT) and different mass wood products, allowing more offsite creation tasks to make use of sustainable and renewable construction substances.
REPORT COVERAGE
The study offers a detailed SWOT analysis and provides valuable insights into future developments within the market. It explores various factors driving market growth, examining a broad range of market segments and potential applications that may shape its trajectory in the coming years. The analysis considers both current trends and historical milestones to provide a comprehensive understanding of the market dynamics, highlighting potential growth areas.
The offsite construction market is poised for significant growth, driven by evolving consumer preferences, rising demand across various applications, and ongoing innovation in product offerings. Although challenges such as limited raw material availability and higher costs may arise, the market's expansion is supported by increasing interest in specialized solutions and quality improvements. Key industry players are advancing through technological advancements and strategic expansions, enhancing both supply and market reach. As market dynamics shift and demand for diverse options increases, the offsite construction market is expected to thrive, with continuous innovation and broader adoption fueling its future trajectory.
Attributes | Details |
---|---|
Market Size Value In |
US$ 120.98 Billion in 2024 |
Market Size Value By |
US$ 186.31 Billion by 2033 |
Growth Rate |
CAGR of 4.9% from 2025 to 2033 |
Forecast Period |
2025-2033 |
Base Year |
2024 |
Historical Data Available |
Yes |
Regional Scope |
Global |
Segments Covered | |
By Type
|
|
By Application
|
FAQs
The Offsite Construction market is expected to reach USD 186.31 billion by 2033.
The Offsite Construction market is expected to exhibit a CAGR of 4.9% by 2033.
Accelerated urbanization to boost the market and the technological advancements in production to expand the market growth
The key market segmentation, which includes, based on type, the offsite construction market is Prefab Construction for Permanent Building, Modular Construction for Relocatable Building. Based on application, the offsite construction market is classified as Residential, Commercial, Industrial.