What is included in this Sample?
- * Market Segmentation
- * Key Findings
- * Research Scope
- * Table of Content
- * Report Structure
- * Report Methodology
Download FREE Sample Report
Orbital Welding Services Market Size, Share, Growth, and Industry Analysis, By Type (flash butt orbital welding, air pressure welded rail, aluminothermic railway welding, and arc welding railway), By Application (subway, high-speed rail, train, and others), Regional Insights and Forecast From 2025 To 2033
Trending Insights
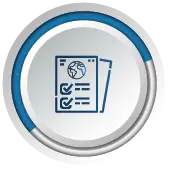
Global Leaders in Strategy and Innovation Rely on Our Expertise to Seize Growth Opportunities
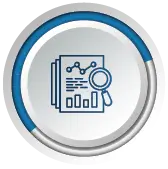
Our Research is the Cornerstone of 1000 Firms to Stay in the Lead
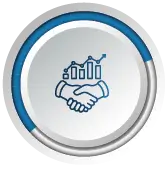
1000 Top Companies Partner with Us to Explore Fresh Revenue Channels
ORBITAL WELDING SERVICES MARKET OVERVIEW
The orbital welding services market size was valued at approximately usd 0.43 billion in 2025 and is expected to reach usd 0.86 billion by 2033, growing at a compound annual growth rate (CAGR) of about 8% from 2025 to 2033
Orbital welding services are a specialised shape of welding that gives precision, consistency, and performance in becoming a member of metallic pipes or tubes. In orbital welding, the welding torch is automatically circled the workpiece, allowing for a continuous, circular weld that conforms precisely to the preferred specifications. This technique is generally used in industries including aerospace, prescription drugs, semiconductor manufacturing, and food and beverage manufacturing, wherein awesome, leak-unfastened welds are vital. One of the number one blessings of orbital welding offerings is their potential to attain excessive stages of accuracy and repeatability, resulting in welds with steady nice and integrity. By removing human error and ensuring unique control over welding parameters consisting of warmth input, tour velocity, and arc duration, orbital welding offerings limit the risk of defects and variability within the completed welds. This is mainly important in industries with stringent satisfactory requirements and regulatory necessities, in which even minor deviations in weld high-quality can have huge outcomes. Furthermore, orbital welding offerings offer productivity profits and fee financial savings as compared to standard guide welding strategies. The automated nature of orbital welding permits faster weld speeds, improved throughput, and reduced labour requirements, main to average lower manufacturing prices and advanced performance. Additionally, the capability to program and save welding parameters permits fast setup and changeover between specific welding jobs, further improving productiveness and versatility. Overall, orbital welding services provide a reliable and efficient solution for achieving top-notch welds in a wide range of industrial applications, making them a desired desire for manufacturers looking to optimize their welding tactics.
COVID-19 IMPACT
Disruptions in supply chains hampered the supply of orbital welding services
The global COVID-19 pandemic has been unprecedented and staggering, with the market experiencing higher-than-anticipated demand across all regions compared to pre-pandemic levels. The sudden market growth reflected by the rise in CAGR is attributable to the market’s growth and demand returning to pre-pandemic levels.
The COVID-19 pandemic has had a first-rate impact on the orbital welding offerings market, providing both challenges and opportunities for corporations running this quarter. Initially, giant lockdowns, tour regulations, and disruptions in supply chains hampered the supply of orbital welding services. Many construction initiatives and business operations were delayed or placed on keep, due to a lower call for for welding services, which includes orbital welding, throughout various industries. Moreover, social distancing measures and fitness worries triggered agencies to put in force far-off work guidelines and restrict on-website sports, similarly affecting the provision of welding services. However, amidst the challenges posed with the aid of the pandemic, the demand for orbital welding services in certain industries remained resilient or maybe accelerated. Sectors consisting of prescription drugs, biotechnology, food processing, and semiconductor production, which depend closely on cleanroom environments and high-purity welding techniques, persisted in requiring specialised welding offerings to guide ongoing operations and meet heightened calls for critical products. Additionally, as industries adapted to the "new normal" and applied measures to ensure peace of job safety and compliance with health recommendations, the importance of automation and far-off-managed welding technologies, along with orbital welding, have become an increasingly number of identified. Furthermore, the COVID-19 pandemic expanded the adoption of digitalization and faraway tracking solutions within the welding enterprise, which include orbital welding services. Companies invested in superior welding gadgets with integrated connectivity capabilities and remote monitoring capabilities, making an allowance for real-time tracking of welding tactics, troubleshooting, and satisfactory warranties from remote locations. This shift toward digitization and automation no longer simplest more desirable operational efficiency and productivity but additionally located welding carrier providers to better navigate destiny disruptions and meet evolving purchaser demands. Overall, whilst the COVID-19 pandemic posed vast challenges for the orbital welding offerings marketplace, it additionally spurred innovation, adaptation, and the popularity of the important function that superior welding technology plays in maintaining business operations and resilience in times of crisis.
LATEST TRENDS
Integration of robotic hands with equipment to bring automation
One of the brand-new traits in the orbital welding services marketplace is the growing adoption of robot orbital welding systems. These superior structures integrate robotic hands with orbital welding equipment, bearing in mind automatic welding procedures in numerous programs. Robotic orbital welding systems offer several advantages, which include superior precision, consistency, and efficiency in welding first-rate and manufacturing throughput. By automating repetitive welding obligations, those systems reduce labour costs, reduce human mistakes, and improve typical productiveness. Moreover, robotic orbital welding structures can gain access to limited spaces and execute complicated weld geometries with no trouble, making them appropriate for a wide variety of industries, inclusive of automobile, aerospace, and production. Another emerging trend in the orbital welding offerings market is the integration of augmented fact (AR) and virtual truth (VR) technology into welding strategies. AR and VR gear offers welders immersive schooling reports, interactive guidance, and real-time remarks throughout welding operations. Welders can visualize welding parameters, joint configurations, and welding sequences overlaid onto their physical environment, enhancing situational recognition and choice-making competencies. Additionally, AR and VR solutions enable faraway collaboration among skilled welders and novice operators, facilitating know-how transfer and talent development. By leveraging AR and VR technologies, welding provider providers can enhance training effectiveness, reduce the studying curve for brand-spanking new welders, and beautify ordinary welding satisfaction and efficiency. Furthermore, sustainability and environmental awareness are increasingly shaping the orbital welding offerings market, using demand for eco-friendly welding solutions and practices. Companies specializing in minimizing material waste, strength intake, and emissions associated with welding strategies whilst maximizing useful resource performance and recyclability. Sustainable welding technologies, along with laser welding and friction stir welding, are gaining traction due to their decreased environmental footprint and reduced reliance on consumables in comparison to standard welding techniques. Additionally, orbital welding carrier vendors are exploring alternative power sources, which include renewable strength assets and battery-operated welding devices, to in addition lessen carbon emissions and sell sustainability. By embracing sustainable welding practices, organizations cannot handiest meet regulatory necessities and company sustainability goals but additionally appeal to environmentally aware customers and stakeholders, positioning themselves as responsible industry leaders in the evolving orbital welding services market.
ORBITAL WELDING SERVICES MARKET SEGMENTATION
By Type
Based on type the market can be categorized into flash butt orbital welding, air pressure welded rail, aluminothermic railway welding, and arc welding railway.
- Flash butt orbital welding: Flash butt orbital welding is a specialised welding method used in general for becoming a member of rail results in railway tracks. This method entails the software of high cutting-edge and stress to fuse the ends of two rails, growing a seamless and sturdy connection. Flash butt orbital welding guarantees top-notch mechanical residences and structural integrity, making it ideal for excessive-velocity railway lines and heavy visitors routes in which tune balance and durability are paramount.
- Air pressure welded rail: Air pressure welded rail, also referred to as pneumatic welding, is any other approach hired for rail joining in railway creation. In this process, rails are heated with the usage of fuel flames or electric induction, and stress is implemented to forge a metallurgical bond among the rail ends. Air stress welded rail offers benefits which include uniform heating, specific manipulation over welding parameters, and minimum distortion. It is normally used for welding rails in continuous welded rail (CWR) installations, ensuring clean and continuous music alignment.
- Aluminothermic railway welding: Aluminothermic welding, also called thermit welding, is an extensively used method for joining rails, specifically in railway preservation and repair programs. This exothermic reaction-primarily based system entails the use of a chemical response between aluminium powder and metallic oxide to provide molten metallic, which fills the gap between rail ends and bureaucracy a strong weld joint. Aluminothermic railway welding offers advantages such as ease of utility, minimum gadget requirements, and suitability for field welding operations.
- Arc welding railway: Arc welding is a versatile welding technique employed in diverse railway packages, which includes music construction, repair, and fabrication. In arc welding railway packages, methods which include shielded metallic arc welding (SMAW), fuel steel arc welding (GMAW), and gas tungsten arc welding (GTAW) may be utilized relying on the precise requirements of the venture. Arc welding gives flexibility in welding specific sorts of rails, joints, and additives, making it appropriate for an extensive range of railway welding duties.
By Application
Based on application the market can be categorized into subway, high-speed rail, train, and others.
- Subway: Applied in joining rail ends for excessive-speed railway lines and heavy site visitors routes to ensure tune balance and toughness.
- High-speed rail: Employed in welding rails for continuous welded rail (CWR) installations to hold clean and non-stop tune alignment.
- Train: Utilized for rail upkeep and restore programs, presenting ease of application and suitability for subject welding operations.
- Others: Applied in various railway tasks, including tune production, repair, and fabrication, imparting flexibility and versatility in welding one-of-a-kind rail kinds and components.
DRIVING FACTORS
Infrastructural development projects increase demand
The ongoing and planned infrastructure improvement initiatives globally, which include new railway strains, expansions, and improvements, pressure calls for railway welding services. Governments and personal investors put money into railway infrastructure to beautify transportation efficiency, connectivity, and potential, main to elevated possibilities for railway welding companies. These initiatives require tremendous welding services for rail tune construction, preservation, and repair, contributing to the increase of the orbital welding service market growth.
Market growth supported by technological advancements in techniques used
Continuous improvements in welding technology, including enhancements in welding gadgets, substances, and methods, force innovation and performance in railway welding. Advanced welding strategies which include flash butt orbital welding, air pressure welding, and aluminothermic welding provide advantages along with improved weld best, productivity, and sturdiness. Railway welding businesses that adopt and leverage these advanced strategies benefit from an aggressive aspect, attracting more customers and increasing their marketplace presence.
RESTRAINING FACTOR
Regulatory compliance and safety standards pose challenges
Railway welding operations are subject to stringent regulatory requirements and safety requirements imposed via government organizations and industry bodies. Compliance with these standards provides complexity and value to railway welding initiatives, as groups have to invest in schooling, certification, and protection measures to ensure compliance. Additionally, regulatory changes or updates might also require modifications in welding practices and methods, leading to operational disruptions and multiplied compliance expenses. Non-compliance with safety and pleasant standards can result in criminal liabilities, mission delays, and reputational damage for railway welding organizations, acting as a restraining issue within the marketplace.
-
Request a Free sample to learn more about this report
ORBITAL WELDING SERVICES MARKET REGIONAL INSIGHTS
Europe to Dominate the Market with continuous advancements and technological developments
The market is primarily segregated into Europe, Latin America, Asia Pacific, North America, and Middle East & Africa.
Europe emerged as a place that dominates the railway welding market, demonstrating vast impact and management in railway infrastructure improvement, innovation, and technological development. Firstly, European countries boast huge and nicely-mounted railway networks, comprising excessive-pace rail lines, city transit structures, and freight corridors. These networks require continuous maintenance, restoration, and modernization, using the demand for railway welding services and answers. Additionally, Europe's commitment to sustainable transportation and funding in railway infrastructure align with worldwide efforts to reduce carbon emissions and promote environmentally friendly modes of transportation, in addition to stimulating an increase within the railway welding marketplace. Secondly, European nations are at the leading edge of technological innovation in railway engineering and welding techniques. European companies lead in the development and adoption of superior welding technology, inclusive of flash butt orbital welding, air strain welding, and aluminothermic welding, which provide superior overall performance, efficiency, and durability in rail construction and protection. Moreover, European research institutions and enterprise consortia collaborate to power innovation in railway welding materials, procedures, and systems, fostering a conducive environment for technological development and marketplace dominance. Furthermore, Europe's regulatory framework and standards for railway safety, satisfaction, and interoperability set the benchmark for railway welding practices globally. The European Union (EU) and European standardization groups establish common technical specs and certification requirements for railway infrastructure and welding products, ensuring uniformity, interoperability, and compliance across European rail networks. These harmonized regulatory surroundings enhance self-belief amongst stakeholders, encourage funding in railway projects, and draw international partnerships and collaborations. As a result, Europe keeps dominating the orbital welding service market share, serving as a hub for understanding, innovation, and excellence in railway engineering and construction.
KEY INDUSTRY PLAYERS
Key Players Transforming the market Landscape through Innovation and setting industrial standards
Key players within the railway welding market play pivotal roles in using innovation, setting industry standards, and presenting complete solutions to meet the various needs of railway infrastructure tasks. Firstly, those key gamers, which encompass distinguished welding device producers, railway production corporations, and welding carrier providers, contribute to advancing welding technology and techniques tailor-made specifically for railway applications. By investing in studies and development, those companies introduce current welding systems, materials, and techniques that decorate the efficiency, high quality, and sturdiness of railway welds. Secondly, key players in the railway welding marketplace play a vital role in project execution and delivery with the aid of imparting cease-to-cease solutions encompassing welding offerings, assignment control, and technical guides. These corporations leverage their understanding and experience to undertake complex railway welding projects, which include track construction, renovation, and restoration. From initial making plans and layout to final inspection and first-rate guarantee, key players provide complete offerings that ensure the integrity, safety, and durability of railway infrastructure. Furthermore, key players serve as drivers of enterprise collaboration and information-sharing initiatives aimed at advancing great practices, requirements, and regulations in railway welding. Through participation in enterprise institutions, boards, and running companies, these organizations contribute to the improvement of consensus-based pointers and certifications that promote safety, niceness, and sustainability in railway welding operations. By fostering a culture of continuous mastering and development, key gamers encourage self-assurance among stakeholders and stakeholders and pressure continuous advancements in railway welding practices. Overall, the position of key gamers inside the railway welding market is instrumental in driving innovation, turning in exquisite solutions, and selling collaboration and excellence across the enterprise. Through their knowledge, resources, and dedication to excellence, these organizations make contributions to the efficient and dependable operation of railway networks worldwide, assisting financial growth, mobility, and connectivity.
List of Top Orbital Welding Services Companies
- Chengdu Aigre Technology (China)
- Plasser and Theurer (Austria)
- Schlatter group (Switzerland)
- Progress Rail (US)
INDUSTRIAL DEVELOPMENT
Oct 2021: One widespread industrial development in the railway welding market happened with the advent of automated robot welding structures specially designed for railway packages. This development happened in October 2021. These advanced robot welding structures are equipped with specialized end-effectors and sensors tailored for welding railway tracks, switches, and components with precision and efficiency. By automating repetitive welding duties, those systems enhance productivity, lessen exertion charges, and beautify weld quality consistency. Additionally, robotic welding structures provide blessings inclusive of multiplied safety, as they reduce human publicity to hazardous welding environments, and more advantageous flexibility, allowing for personalization and variation to diverse railway welding requirements. This business development represents an extensive milestone in the evolution of railway welding generation, offering railway creation groups and protection carriers new possibilities to streamline operations and improve standard efficiency and great in railway welding tasks.
REPORT COVERAGE
This report is based on historical analysis and forecast calculation that aims to help readers get a comprehensive understanding of the global Orbital Welding Services market from multiple angles, which also provides sufficient support to readers’ strategy and decision-making. Also, this study comprises a comprehensive analysis of SWOT and provides insights for future developments within the market. It examines varied factors that contribute to the growth of the market by discovering the dynamic categories and potential areas of innovation whose applications may influence its trajectory in the upcoming years. This analysis encompasses both recent trends and historical turning points into consideration, providing a holistic understanding of the market’s competitors and identifying capable areas for growth.
This research report examines the segmentation of the market by using both quantitative and qualitative methods to provide a thorough analysis that also evaluates the influence of strategic and financial perspectives on the market. Additionally, the report's regional assessments consider the dominant supply and demand forces that impact market growth. The competitive landscape is detailed meticulously, including shares of significant market competitors. The report incorporates unconventional research techniques, methodologies and key strategies tailored for the anticipated frame of time.
Attributes | Details |
---|---|
Market Size Value In |
US$ 0.43 Billion in 2024 |
Market Size Value By |
US$ 0.86 Billion by 2033 |
Growth Rate |
CAGR of 8% from 2025 to 2033 |
Forecast Period |
2025 - 2033 |
Base Year |
2024 |
Historical Data Available |
Yes |
Regional Scope |
Global |
Segments Covered |
|
By Type
|
|
By Application
|
FAQs
Europe dominates the Orbital Welding Services Market with continuous advancements and technological developments.
The driving factors of the Orbital Welding Services Market are Infrastructural development projects increased demand, and Market growth supported by technological advancements in techniques used.
The Orbital Welding Services market segmentation that you should be aware of, includes, based on type: flash butt orbital welding, air pressure welded rail, aluminothermic railway welding, and arc welding railway. Based on the application: flash butt orbital welding, air pressure welded rail, aluminothermic railway welding, and arc welding railway.
The global orbital welding services is expected to reach USD 0.86 billion by 2033.
The orbital welding services is expected to exhibit a CAGR of 8% by 2033.