What is included in this Sample?
- * Market Segmentation
- * Key Findings
- * Research Scope
- * Table of Content
- * Report Structure
- * Report Methodology
Download FREE Sample Report
Pre-engineered building Market Size, Share, Growth, and Industry Analysis, By Type (Industrial Sheds, Warehouses, Aircraft Hangars, Commercial Complexes and Cold Storage), By Application (Industrial, Commercial, Infrastructure, Logistics and Agricultural), and Regional Insights and Forecast to 2033
Trending Insights
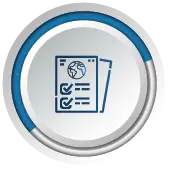
Global Leaders in Strategy and Innovation Rely on Our Expertise to Seize Growth Opportunities
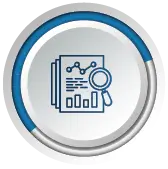
Our Research is the Cornerstone of 1000 Firms to Stay in the Lead
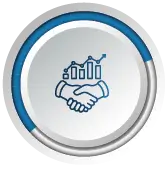
1000 Top Companies Partner with Us to Explore Fresh Revenue Channels
PRE-ENGINEERED BUILDING MARKET OVERVIEW
The global pre-engineered building market size was USD 18.73 billion in 2025 and is projected to touch USD 28.05 billion by 2033, exhibiting a CAGR of 5.18% during the forecast period.
Pre-engineered buildings (PEBs) are modern construction results where building factors are designed, fabricated and assembled out- point before being transported for quick on- point installation. These structures use formalized, high- strength sword frames and are acclimatized to specific confines and functions, making them cost-effective and time-effective. PEBs are extensively used in storages, manufactories, marketable spaces, and agrarian installations due to their continuity, scalability, and design inflexibility. They offer benefits like reduced construction time, minimum waste, and lower conservation costs. As industrialization and structure development rise, PEBs are getting decreasingly popular for their effectiveness, sustainability, and rigidity to different environmental and functional conditions.
The pre ‑ engineered building (PEB) market is accelerating encyclopedically, fueled by demand for rapid, cost ‑ effective construction and sustainable design results. Urbanization and structure growth are pushing governments and the private sector to borrow PEBs for storages, marketable spaces, and conveyance capitals due to their quick on- point assembly and reduced waste. Meanwhile, sustainability enterprise and energy- effectiveness authorizations are egging inventors to choose PEBs equipped with insulated panels, reflective roofs, and eco-friendly materials. Also, technological advances similar as CAD/ BIM design, automated fabrication, and IoT integration — are enhancing customization, structural perfection, and structure performance, buttressing the appeal of PEBs in modern construction.
COVID-19 IMPACT
Pre-engineered building Industry had a negative Effect Due to lockdown restrictions during COVID-19 Pandemic
The global COVID-19 pandemic has been unprecedented and staggering, with the market experiencing lower-than-anticipated demand across all regions compared to pre-pandemic levels. The sudden market growth reflected by the rise in CAGR is attributable to the market’s growth and demand returning to pre-pandemic levels.
The epidemic caused significant dislocations in the pre ‑ finagled building (PEB) sector. Lockdowns and travel restrictions led to force chain breakdowns, raw material alternatives, and elevated costs especially for sword — delaying systems and pushing supereminent times 25 – 40% longer. Construction exertion braked due to labor alternatives and social distancing rules, stalling numerous enterprises. Still, demand also surged for fleetly deployable installations like mobile hospitals, counter blockade units, and logistics capitals, showcasing PEB’s rigidity. The extremity accelerated digital invention — BIM, remote operation, and modular prefabrication — cementing PEBs as effective, flexible post-pandemic construction results
LATEST TRENDS
Integration of Smart & Digital Technologies to Drive Market Growth
Recent traits inside the pre-engineered building industry include the integration of smart and digital technologies to enhance design, construction, and operation. Advanced Building Information Modeling (BIM), digitalization, and IoT detectors are now essential tools for perfection engineering, real- time collaboration, and visionary structure operation. IoT- enabled monitoring systems collect data on temperature, humidity, and structural integrity, enabling prophetic conservation and energy optimization. Also, digitalization in fabrication and robotic assembly accelerates construction timelines, lowers labour costs, and improves quality control. This digital metamorphosis is reshaping PEB relinquishment, situating it as a tech ‑ driven, effective construction result for modern buildings.
PRE-ENGINEERED BUILDING MARKET SEGMENTATION
By Type
Based on Type, the global market can be categorized into Industrial Sheds, Warehouses, Aircraft Hangars, Commercial Complexes and Cold Storage
- Industrial Sheds: Industrial sheds are large, durable structures used for storehouse, manufacturing, and logistics operations. Generally erected using sword fabrics, they offer commodious, flexible layouts suitable for heavy ministry and bulk goods. Pre-engineered designs insure quick construction, cost effectiveness, and customization, making them essential for artificial, warehousing, and structure development systems.
- Warehouses: Storages are storehouse installations designed to house goods, raw materials, and finished products before distribution or use. They play a pivotal part in force chain and force operation. Modern storages frequently feature digitalization, climate control, and advanced security, supporting diligence like retail, manufacturing, and e-commerce with effective storehouse and logistics results.
- Aircraft Hangars: Aircraft hangars are large, enclosed structures designed to house and cover aeroplanes from weather and environmental damage. They give space for conservation, form, and storehouse of aircraft. Erected with durable materials like sword, hangars are essential in aeronautics structure, ensuring safety, availability, and functional effectiveness at airfields and airbases.
- Commercial Complexes: Commercial complexes are multi-purpose structures that house businesses, services, retail stores, and service providers in a centralized position. Designed for high footfall and effective space use, they support profitable exertion and civic development. These complexes frequently feature ultramodern amenities, ample parking, and availability, making them crucial capitals in marketable zones.
- Cold Storage: Cold Storehouse installations are temperature- controlled storages used to save perishable goods like fruits, vegetables, dairy, meat, and medicinals. By maintaining low temperatures, they extend product shelf life and insure quality during storehouse and transportation. Cold storehouse is essential for food safety, force chain effectiveness, and reducing post-harvest and force losses.
By Application
Based on Application, the global market can be categorized into Industrial, Commercial, Infrastructure, Logistics and Agricultural
- Industrial: It offers presto, cost-effective results for manufactories, storages, and product units. These sword structures are designed for continuity, large clear spans, and easy customization. Their quick installation, low conservation, and rigidity make them ideal for meeting the growing demands of artificial structure and operations.
- Commercial: in the commercial sector give effective, scalable results for services, retail outlets, and shopping complexes. These structures offer rapid construction, modern aesthetics, and flexible interior layouts. With cost-effective design and energy-effective features, they're ideal for businesses seeking durable, functional, and quickly deployable commercial building.
- Infrastructure: Pre-engineered building in infrastructure support systems like airfields, road stations, islands, and logistics capitals by offering presto, durable, and scalable construction Their prefabricated sword factors insure quick assembly, structural trustability, and reduced labour costs. These structures enhance design effectiveness and are pivotal for contemporizing public structure efficiently and economically.
- Logistics: It gives effective solutions for storages, distribution centers, and storehouse installations. Their quick installation, large clear spans, and customizable layouts support smooth goods movement and force operation. These structures enhance functional effectiveness; reduce construction time, and offer cost-effective, durable structure essential for ultramodern force chain operations.
- Agricultural: It offers durable, cost-effective results for barns, storehouse sheds, and livestock shelters. Designed for quick assembly and weather resistance, they support crop storehouse, ministry casing, and animal protection. Their flexible layouts and low conservation needs make them ideal for enhancing productivity and effectiveness in agricultural operations.
MARKET DYNAMICS
Market dynamics include driving and restraining factors, opportunities and challenges stating the market conditions.
Driving Factors
Rapid Urbanization and Industrial Growth to Aid Market Growth
A factor in the pre-engineered building market growth is the accelerating pace of urbanization and industrial development. As cities expand and new artificial zones crop, there's a rising need for quick, scalable, and cost-effective construction results. PEBs fulfill these demands by offering faster construction timelines, reduced labour conditions, and high design inflexibility. Their capability to be customized for storages, manufactories, and commercial spaces makes them ideal for supporting civic and artificial structure. Governments and private inventors increasingly borrow PEBs to meet tight design schedules and growing space demands in expanding civic geographies.
Demand for Sustainable and Energy-Efficient Construction to Drive Market Growth
The demands for sustainable and energy-efficient construction are another key aspect of the pre-engineered building market. Growing environmental mindfulness and stricter sustainability regulations are fueling demand for eco-friendly structure practices, pushing the relinquishment of pre-engineered building. PEBs are known for their energy effectiveness, minimum waste generation, and comity with green accoutrements and technologies. Features like insulated panels, reflective roofing, and solar-ready designs help reduce energy consumption and environmental impact. Also, off- point fabrication limits on- point disturbances and carbon emigrations. As sustainability becomes precedence in construction planning, inventors, engineers, and governments prefer PEBs to align with green building instruments and long- term environmental pretensions. This trend significantly contributes to the rising fashionability of PEBs across sectors.
Restraining Factor
Limited Awareness and Acceptance in Certain Regions to Restrain Market Progress
The limited awareness and acceptance in certain regions, especially in rural or traditionally built-up areas poses a significant restraining factor for the growth of the pre-engineered building market. Numerous inventors and guests remain strange with the benefits and capabilities of PEBs, frequently preferring conventional construction styles due to habit or lack of exposure. This disinclination can be linked to misconceptions about the continuity, design inflexibility, or long- term performance of PEBs. Also, shy marketing sweats and inadequate training for original contractors further hamper relinquishment. Prostrating this hedge requires education, demonstration systems, and collaboration to make trust in PEB technology.
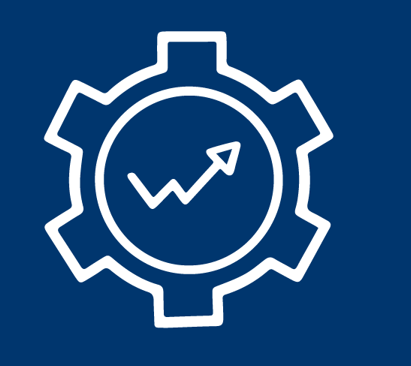
Rising Demand in Emerging Economies to Create Opportunity for the Product in the Market
Opportunity
A major opportunity in the pre-engineered building (PEB) market lies in the growing demand from arising economic. Rapid urbanization, artificial expansion, and structure development in regions like Asia, Africa, and Latin America are driving the need for presto, cost-effective construction results. PEBs offer an ideal fit due to their quick assembly, scalability, and lower resource consumption.
Governments in these regions are also investing in artificial premises, logistics capitals, and smart cities, creating a favourable environment for PEB relinquishment. By offering localized designs, affordable pricing, and effective force chains, companies can tap into these high- growth markets and expand their global footmark.
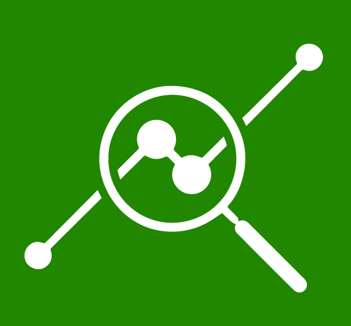
Fluctuating Raw Material Prices and Supply Chain Disruptions Could Be a Potential Challenge for Consumers
Challenge
A significant challenge in the pre-engineered building (PEB) market is the change in raw material prices, particularly sword, which is a primary element in PEB structures. Unforeseen price hikes can increase overall design costs, affecting profitability and pricing strategies. Also, global force chain dislocations caused by geopolitical pressures, afflictions, or transportation backups — can delay material vacuity and design timelines.
These misgivings make it delicate for manufacturers and builders to plan effectively, frequently leading to cost overruns or missed deadlines. To alleviate this, companies must borrow flexible sourcing strategies, maintain force buffers, and explore indispensable accoutrements or localized force networks when feasible.
-
Request a Free sample to learn more about this report
PRE-ENGINEERED BUILDING MARKET REGIONAL INSIGHTS
-
North America
The region dominates the pre-engineered building market share. North America leads the global pre-engineered building (PEB) market, landing nearly one- third of profit in 2024. The United States generated roughly USD 4.6 billion, about 37.5% of worldwide affair, while the region overall reached USD 5.2 billion. Fueling this dominance are surging e-commerce investments, extensive artificial and storehouse constructions, and strong out- point structure relinquishment. Technological integration — similar as CAD/ BIM, automated fabrication, and sustainable, energy-effective accoutrements — further enhances PEB appeal. Robust cold chain and logistics structure, along with large- scale single- story artificial demand; fortify North America’s leadership in effective, scalable, and eco-conscious construction results.
-
Europe
Europe’s pre-engineered building (PEB) market is expanding steadily, driven by sustainability authorizations and civic redevelopment systems. Regulatory fabrics like the EU Green Deal encourage low ‑ carbon, energy ‑ effective structures, egging inventors in Germany, the UK, and France to borrow PEBs for marketable and structure uses. Modular construction styles offer rapid-fire assembly, design inflexibility, and reduced waste — appealing to metropolises targeting briskly design delivery and lower environmental impact. also, artificial demand is growing, with PEBs serving storages, logistics capitals, and manufacturing installations thanks to scalable clear ‑ span designs and favourable economics. As Europe presses ahead with green structure and structure modernization, PEB relinquishment is poised to accelerate.
-
Asia
Asia’s pre-engineered building (PEB) market is expanding fleetly, propelled by urbanization, industrialization, and large- scale structure development. In China and India — the market’s boot-strappers — new artificial corridors, smart cities, and logistics capitals are driving demand for presto, cost-effective construction results using PEBs. E ‑ commerce thunderclaps in Southeast Asian nations similar as Vietnam, Indonesia, and Thailand farther energy demand for marketable installations and storages erected with scalable, clear- span PEB designs. The region leads encyclopedically in PEB relinquishment, supported by low labor costs, favourable programs, and investments from major manufacturers. As profitable and digital structure contemporize, Asia looks poised for continued PEB market dominance.
KEY INDUSTRY PLAYERS
Key Industry Players Shaping the Market through Innovation and Market Expansion
Key enterprise players are shaping the pre-engineered building marketplace through strategic innovation and marketplace growth. These agencies are introducing superior milling strategies to beautify the fine and nutritional profile. They are also increasing their product traces to include specialized versions like organic and vertical farming, catering to various purchaser preferences. Additionally, they may be leveraging virtual systems for greater market reach and distribution performance. By making an investment in research and improvement, improving delivery chain managements, and exploring new regional markets, those players are riding a boom and setting traits within the pre-engineered building enterprise.
List Of Top Pre-Engineered Building Companies
- BlueScope (Australia)
- Nucor (USA)
- Kirby Building Systems (Kuwait)
- Zamil Steel (Saudi Arabia)
- Everest Industries (India)
- Tata Steel (India)
- Lindab (Sweden)
- ATCO (Canada)
- PEBS Pennar (India)
- Jindal Buildsys (India)
KEY INDUSTRIAL DEVELOPMENT
July 2024: Pennar Industries Limited has announced the opening of a new manufacturing facility in Raebareli, Uttar Pradesh. Spanning 16 acres with a built-up area of 12,000 square meters, the plant will have an annual production capacity of 36,000 metric tons. This strategic expansion is designed to cater to rising demand in Northern and Eastern India while optimizing logistics and reducing transportation costs, thereby enhancing overall operational efficiency and strengthening the company's presence in key regional markets.
REPORT COVERAGE
The study encompasses a comprehensive SWOT analysis and provides insights into future developments within the market. It examines various factors that contribute to the growth of the market, exploring a wide range of market categories and potential applications that may impact its trajectory in the coming years. The analysis takes into account both current trends and historical turning points, providing a holistic understanding of the market's components and identifying potential areas for growth.
The research report delves into market segmentation, utilizing both qualitative and quantitative research methods to provide a thorough analysis. It also evaluates the impact of financial and strategic perspectives on the market. Furthermore, the report presents national and regional assessments, considering the dominant forces of supply and demand that influence market growth. The competitive landscape is meticulously detailed, including market shares of significant competitors. The report incorporates novel research methodologies and player strategies tailored for the anticipated timeframe. Overall, it offers valuable and comprehensive insights into the market dynamics in a formal and easily understandable manner.
Attributes | Details |
---|---|
Market Size Value In |
US$ 18.73 Billion in 2024 |
Market Size Value By |
US$ 28.05 Billion by 2033 |
Growth Rate |
CAGR of 5.18% from 2025 to 2033 |
Forecast Period |
2025-2033 |
Base Year |
2024 |
Historical Data Available |
Yes |
Regional Scope |
Global |
Segments Covered |
|
By Type
|
|
By Application
|
FAQs
The global pre-engineered building market is expected to reach 28.05 billion by 2033.
The pre-engineered building market is expected to exhibit a CAGR of 5.18% by 2033.
The accelerating pace of urbanization and industrial development and demands for sustainable and energy-efficient construction are some of the driving factors in the market.
The key market segmentation, which includes, based on type, the Pre-engineered building market is classified as Industrial Sheds, Warehouses, Aircraft Hangars, Commercial Complexes and Cold Storage. Based on application, the pre-engineered building market is classified as Industrial, Commercial, Infrastructure, Logistics and Agricultural.