What is included in this Sample?
- * Market Segmentation
- * Key Findings
- * Research Scope
- * Table of Content
- * Report Structure
- * Report Methodology
Download FREE Sample Report
Welding Consumables Market Size, Share, Growth, and Market Analysis ByType (Stick Electrodes, Solid Wires, Flux Cored Wires, SAW Wires & Fluxes), By Application (Automotive, Construction, Aerospace & Defense, Shipbuilding, Pipe, Others), and Regional Insight and Forecast to 2033
Trending Insights
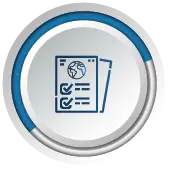
Global Leaders in Strategy and Innovation Rely on Our Expertise to Seize Growth Opportunities
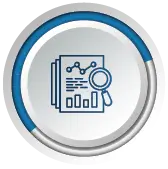
Our Research is the Cornerstone of 1000 Firms to Stay in the Lead
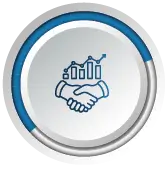
1000 Top Companies Partner with Us to Explore Fresh Revenue Channels
WELDING CONSUMABLES MARKET OVERVIEW
The Welding Consumables Market stood at USD 10.75 billion in 2024 and is set to expand to USD 11.07 billion in 2025, eventually reaching USD 14.29 billion by 2033, driven by a CAGR of 2.8%.
The welding consumables industry is an essential component of the world's industrial manufacturing landscape and is an indispensable facilitator for the fabrication operations across the wide-ranging industries such as construction, the automotive industry, shipbuilding, and the development of the energy infrastructure. These consumables – electrodes, wires, fluxes, shielding gases – are special materials that make up the critical intermediate link between welding devices and base metals, which in turn reflect joint quality (integrity), mechanical properties, and even macroscopic structure performance. Economic dynamics are closely related to industrial activities at large and are highly correlated with infrastructure investment cycles, the trend of manufacturing output, and the development of heavy industry.
The relatively low growth rate of this sector reflects its maturity and well‐established technology base, but continuous material and consumable innovation, especially for advanced alloys and demanding applications, continues to provide development opportunities that improve the performance of the process and the market value proposition. The competitive landscape in this industry is a mixture of consolidation among large global manufacturers and regional specialization, with large multinational corporations dominating market share with a wide range of product offerings and smaller, regional specialty manufacturers serving niche applications and local market needs. This structure not only achieves economies of scale in the production of standard consumables, but it can also deliver tailored solutions to meet specific welding needs, and provides an even level of competition for multiple customer segments.
COVID-19 IMPACT
Welding Consumables Industry Had a Negative Effect Due to Manufacturing Disruptions During the COVID-19 Pandemic.
The global COVID-19 pandemic has been unprecedented and staggering, with the market experiencing lower-than-anticipated demand across all regions compared to pre-pandemic levels. The sudden growth reflected by the rise in CAGR is attributable to the market's growth and demand returning to pre-pandemic levels.
The pandemic created large operational demanding situations at some point of the welding consumables price chain, disrupting uncooked cloth substances, production operations, and distribution networks. Production facilities confronted workforce barriers because of social distancing requirements and fitness-associated absenteeism, reducing manufacturing capacity and growing periodic product shortages in certain marketplace segments. International logistics disruptions concurrently impacted each uncooked material import and completed product distribution, especially affecting cross-border delivery chains and creating stock control challenges for both producers and vendors.
Recovery patterns emerged inconsistently throughout areas and application sectors, with infrastructure stimulus applications in certain nations accelerating creation and heavy industry activity that partially offset ongoing weaknesses in different segments. Manufacturers with diverse global market exposure established extra resilience, particularly those with a sizable presence in sectors categorized as essential industries during pandemic regulations. The crisis multiplied several pre-existing market developments, which include a more suitable consciousness on supply chain regionalization, elevated adoption of digital distribution channels, and developing emphasis on technical carrier offerings that provide remote help competencies.
LATEST TRENDS
Advanced Consumables for New-Generation Materials to Drive Market Growth
Advanced consumables for new-generation materials are vital benefits of Welding Consumables market share. The improvement and commercialization of specialized welding consumables designed specifically for subsequent-era substances represents a defining marketplace fashion with giant growth implications. These superior consumables address the increasingly complicated needs of high-performance alloys, ultra-high-strength steels, and lightweight materials, which can be adopted throughout transportation, power, and advanced production sectors. In the automobile industry, the transition closer to blended-cloth car systems incorporating advanced high-electricity steels, aluminum components, and composite materials has created a call for consumables that can correctly join distinctive substances while maintaining vital protection and performance characteristics. Similarly, aerospace production is predicated on specialized consumables capable of developing high-integrity joints in titanium alloys, nickel superalloys, and advanced aluminum formulations utilized in aircraft structures and propulsion systems
WELDING CONSUMABLES MARKET SEGMENTATION
By Type
Based on Type, the global welding consumables market can be categorized into Stick Electrodes, Solid Wires, Flux Cored Wires, and SAW Wires & Fluxes.
- Stick Electrodes: Also known as shielded metallic arc welding (SMAW) electrodes, these include a metallic center cord covered with flux compounds that provide arc stabilization, protection, and alloying factors in the course of welding operations.
- Solid Wires: Utilized basically in gas metal arc welding (GMAW/MIG) processes, these continuous cord electrodes require outside shielding gas and offer high deposition performance.
- Flux Cored Wires: These tubular wires contain inner flux compounds that provide defensive and decorative weld residues, available in self-shielded and gas-shielded forms, with particular benefits in outdoor programs, out-of-role welding, and situations requiring better deposition rates than solid core alternatives.
- SAW Wires & Fluxes: Submerged arc welding (SAW) consumables include specialised wires used alongside granular flux substances that absolutely cover the weld pool, permitting extremely high deposition rates.
By Application
Based on Application, the global welding consumables market can be categorized into Automotive, Construction, Aerospace & Defense, Shipbuilding, Pipe, and Others.
- Automotive: The automobile quarter utilizes welding consumables drastically in vehicle body manufacturing, chassis additives, and powertrain assembly, with increasing emphasis on specialised consumables for advanced high-strength steels.
- Construction: Construction programs represent a good-sized consumption sector, with welding consumables utilized in structural steel frameworks, infrastructure projects, and system fabrication, requiring merchandise that supplies dependable performance across diverse environmental conditions and task specs.
- Aerospace & Defense: This excessive-cost phase needs premium welding consumables capable of meeting rigorous fine requirements and specialized cloth meeting requirements for aircraft structures, engine additives, and protection equipment.
- Shipbuilding: Marine vessel production involves widespread welding operations beneath difficult conditions, requiring consumables with awesome crack resistance, sturdy mechanical properties in thick sections, and corrosion resistance competencies for each traditional metallic and specialized alloy packages in hull structures and propulsion structures.
- Pipe: Pipeline construction and fabrication of pipe structures for energy, petrochemical, and water infrastructure constitute a specialised software section requiring consumables optimized for positional welding, high joint integrity, and consistent performance under various conditions.
MARKET DYNAMICS
Driving Factor
Infrastructure Development and Urbanization Trends to Boost the Market
A factor in the Welding Consumables market growth is infrastructure development and urbanization trends. Global infrastructure development initiatives and accelerating urbanization developments constitute fundamental growth drivers for the welding consumables market, developing a good-sized call for across production, transportation networks, and software structures globally. Large-scale infrastructure applications in developing economies all through Asia-Pacific, Latin America, and Africa are producing significant consumption of structural metal and associated welding merchandise for bridges, commercial buildings, and business facilities that support increasing city facilities and economic improvement. The ongoing international transition in the direction of renewable electricity infrastructure—including wind towers, solar mounting systems, and hydroelectric centers—has emerged as a particularly dynamic boom phase requiring considerable welding consumable volumes throughout the creation stages.
Rising Focus on Lightweight Material Adoption to Expand the Market
The accelerating adoption of lightweight substances across transportation, energy, and business gadget sectors is creating giant opportunities for specialised welding consumables that could effectively be part of these advanced substances whilst keeping critical overall performance characteristics. Automotive manufacturers are more and more incorporating aluminum alloys, superior high-energy steels, and blended-cloth designs to reduce car weight and enhance gas performance, growing call for for consumables especially engineered for those difficult becoming a member of applications. Similarly, aerospace production relies heavily on titanium alloys, advanced aluminum formulations, and forte steels that require precisely formulated welding consumables to create high-integrity structural connections, assembly rigorous safety and performance standards.
Restraining Factor
Price Sensitivity and Commoditization Pressures to Potentially Impede Market Growth
The welding consumables market faces significant constraints related to price sensitivity and commoditization pressures, particularly within standard product categories that represent substantial volume segments. Many end-users, especially in general fabrication and construction applications, prioritize cost considerations in purchasing decisions, treating standard consumables as commodity inputs and applying significant pricing pressure through competitive bidding processes and contract negotiations. This pricing dynamic limits margin potential for manufacturers and constrains investment capacity for research and product development initiatives that could otherwise accelerate market innovation. The widespread availability of imported products from low-cost manufacturing regions further intensifies pricing competition, particularly for common electrode and wire types with standardized specifications and limited technical differentiation. Distribution channel evolution has further increased price transparency through digital platforms and purchasing aggregation strategies, enabling more aggressive price comparisons and negotiations by end-users.
Opportunity
Integration with Industry 4.0 and Automated Welding Systems To Create Opportunity for the Product in the Market
The accelerating implementation of advanced Industry 4.0 technologies and expanding adoption of automated welding systems provide significant growth opportunities for the welding consumables market, especially through the introduction of specialized products optimized for robotic and automated applications. As manufacturing industries rapidly adapt to accommodate digitally integrated production system infrastructures, welding processes are becoming integrated into connected factory environments requiring repeatable performance, real-time quality assurance and control, and maximum productivity from all system components and weld consumables. The advanced data integration power of current manufacturing platforms are at the same time allowing far deeper tracking and quality tracking of consumable use, opening up possibilities for manufacturers to provide digital services such as inventory control, consumption analysis, and predictive quality systems that improve customer relationships outside of tangible products.
Challenge
Skilled Labor Shortages and Welding Process Changes Could Be a Potential Challenge for Consumers
The welding enterprise faces massive challenges associated with persistent professional hard work shortages and associated welding manner evolutions that notably effect consumable choice, application practices, and performance necessities. The structural deficit of certified welders across most evolved economies has multiplied the adoption of welding tactics and strategies that may be carried out with much less specialized operator skill, together with transitioning from stick electrode techniques toward semi-computerized wire strategies that generally require different consumable sorts and formulations. This personnel quandary is concurrently using expanded automation implementation, which needs consumables with improved consistency and particular performance traits appropriate for robot applications. Training obstacles frequently bring about less optimized consumable choice and application strategies which could impact productivity, first-class, and universal welding economics in spite of advances in product formulations and operational guidance.
-
Request a Free sample to learn more about this report
WELDING CONSUMABLES MARKET REGIONAL INSIGHTS
-
North America
North America is the fastest-growing region in this market. The United States Welding Consumables market has been growing exponentially for multiple reasons. The area's welding consumables marketplace is famous for numerous specific characteristics, including a high penetration of top-class and specialized merchandise that enhance productivity and performance in computerized packages. Wire-based processes constitute a larger percentage of overall intake compared to international averages, reflecting the region's high automation levels and emphasis on manufacturing efficiency in production environments. Distribution channels are tremendously consolidated, with the most important commercial distributors and welding strong point dealers controlling sizeable marketplace share, though direct income relationships remain important for large-volume customers in automotive, power, and heavy system sectors. Environmental policies and administrative center safety necessities increasingly impact product formulations, with growing demand for reduced-fume consumables and merchandise with lower manganese emissions that enhance administrative center conditions in production centers.
-
Europe
The European welding consumables market presents unique regional traits shaped by its various manufacturing industries, strong emphasis on technical standards, and focus on precision engineering programs. The location continues to have enormous manufacturing capability for both general and specialized consumables, with manufacturers in Germany, Italy, Sweden, and other international locations recognized for superb products serving both local demands and export markets worldwide. Premium and specialized consumable segments constitute a good-sized part of the entire marketplace value, reflecting the place's concentration of high-cost manufacturing in sectors including car, aerospace, power device, and business equipment production that require advanced joining technologies. Technical requirements and certification requirements notably affect market dynamics, with specific emphasis on consumable qualifications for critical applications, including pressure vessels, structural components, and protection-critical structures governed via harmonized European standards and industry-unique requirements.
-
Asia
Asia represents the most important and dynamic local marketplace for welding consumables, characterized by a significant volume increase, increasing business competencies, and evolving pleasant requirements across growing and mature production economies. China dominates regional consumption with the world's biggest welding marketplace by extent, supported by considerable production activities in creation, heavy industry, shipbuilding, automotive production, and well-known commercial programs.Regional manufacturing ability has multiplied significantly, with considerable investments in manufacturing centers for both preferred and specialised consumables, creating a shifting, aggressive landscape that serves an increasing number of local necessities and export markets worldwide. Market traits range substantially across the area, with mature industrial economies, along with Japan and South Korea, focused on high-performance consumables for automatic programs and superior materials, whilst growing markets demonstrate extra cost sensitivity and emphasis on trendy product categories for creation and fundamental production.
KEY INDUSTRY PLAYERS
Key Industry Players Shaping the Market Through Innovation and Market Expansion
Key industry players are shaping the welding consumables market through strategic innovation and market expansion initiatives focused on addressing evolving application requirements and enhancing customer value propositions. These companies are developing advanced consumable formulations optimized for specific industry challenges, including specialized alloys for critical applications, high-productivity products for automated systems, and consumables engineered for new-generation materials being adopted across manufacturing sectors. They are diversifying their product portfolios beyond traditional consumables to include integrated welding solutions incorporating digital technologies, technical services, and application engineering capabilities that strengthen customer relationships and create differentiated market positions. Additionally, these organizations are strategically expanding global manufacturing footprints through capacity investments in high-growth regions while simultaneously strengthening application development resources that enhance regional customization capabilities and responsiveness to local market requirements. By implementing digitally-enabled quality systems, developing sustainable manufacturing processes, and creating comprehensive technical support networks, these players are driving both technological advancement and market growth across the welding industry landscape.
List Of Top Welding Consumables Companies
- Lincoln Electric (U.S.)
- Colfax (U.S.)
- Golden Bridge (China)
- Tianjin Bridge (China)
- Voestalpine (Austria)
- ITW (U.S.)
- Kobelco (Japan)
- Weld Atlantic (U.S.)
KEY INDUSTRY DEVELOPMENT
January 2024: Lincoln Electric, a global leader in welding equipment and consumables, announced the commercialization of its next-generation aluminum welding wire system designed specifically for advanced automotive manufacturing applications. The integrated solution combines specialized aluminum filler materials with digital process controls that optimize parameters in real-time based on material conditions and joint configurations.
REPORT COVERAGE
The study offers a detailed SWOT analysis and provides valuable insights into future developments within the market. It explores various factors driving market growth, examining various market segments and potential applications that may shape its trajectory in the coming years. The analysis considers both current trends and historical milestones to provide a comprehensive understanding of the market dynamics, highlighting potential growth areas.
The Welding Consumables market is poised for significant growth, driven by evolving consumer preferences, rising demand across various applications, and ongoing innovation in product offerings. Although challenges such as limited raw material availability and higher costs may arise, the market's expansion is supported by increasing interest in specialized solutions and quality improvements. Key industry players are advancing through technological advancements and strategic expansions, enhancing both supply and market reach. As market dynamics shift and demand for diverse options increases, the Welding Consumables market is expected to thrive, with continuous innovation and broader adoption fueling its future trajectory.
Attributes | Details |
---|---|
Market Size Value In |
US$ 10.75 Billion in 2024 |
Market Size Value By |
US$ 14.29 Billion by 2033 |
Growth Rate |
CAGR of 2.8% from 2025 to 2033 |
Forecast Period |
2025-2033 |
Base Year |
2024 |
Historical Data Available |
yes |
Regional Scope |
Global |
Segments Covered |
|
By Type
|
|
By Application
|
FAQs
Infrastructure Development and Urbanization Trends to boost the market and Rising Focus on Lightweight Material Adoption to expand the Welding Consumables market growth.
The key market segmentation, which includes, based on type, the Welding Consumables market is Stick Electrodes, Solid Wires, Flux Cored Wires, and SAW Wires & Fluxes. Based on application, the Welding Consumables market is classified as Automotive, Construction, Aerospace & Defense, Shipbuilding, Pipe, and Others.
The Welding Consumables Market is expected to reach USD 14.29 billion by 2033.
The Welding Consumables Market is expected to exhibit a CAGR of 2.8% by 2033.